常州机加工系统哪家不错
MES(manufacturingexecutionsystem)是制造执行系统,是一套面向制造企业车间执行层的生产信息化管理系统。MES可以为企业提供包括制造数据管理、计划排程管理、生产调度管理、库存管理、质量管理、生产过程控制、底层数据集成分析、上层数据集成分解等管理模块。MES的概念在90年代由美国AMR公司提出,主要针对于生产制造过程中流程、资源的管理系统,1997年,MESA提出的MES功能组件和集成模型,包括11个功能,同时规定,只要具备11个功能之中的某一个或几个,也属MES系列的单一功能产品。西南电梯电缆行业软件系统供应商众和昊天。常州机加工系统哪家不错
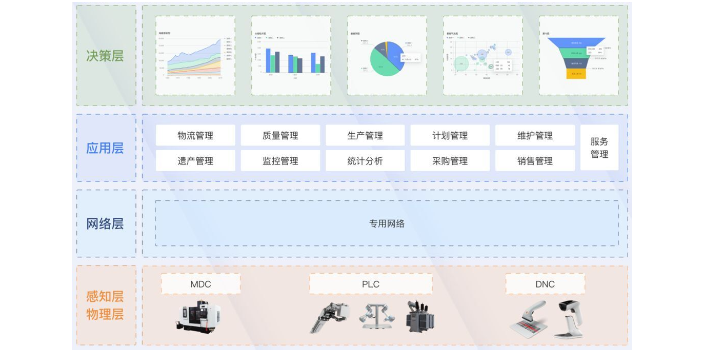
mes系统的重心在于对生产业务的建模,反应现场实时情况,进而警示哪些计划中的事情没有发生,以及发生了哪些计划之外的情况,而不是什么提升效率,降低成本,提升oee,这些事情mes软件是办不到的,它还是要工厂管理者和工程师去搞。至于对工艺管理,品质管理,设备管理这些职能的辅助,则都是建模实现之后的结果,而不是说这些就是mes的功能,这样讲给人感觉是它们好像一个一个是割裂开一样,并不是工厂事实。单独去做这些,对于提升产品的整体效率和质量未必有效,甚至有时候还会额外增加生产负担。江苏设备联网系统品牌江苏机加工行业软件系统供应商众和昊天。
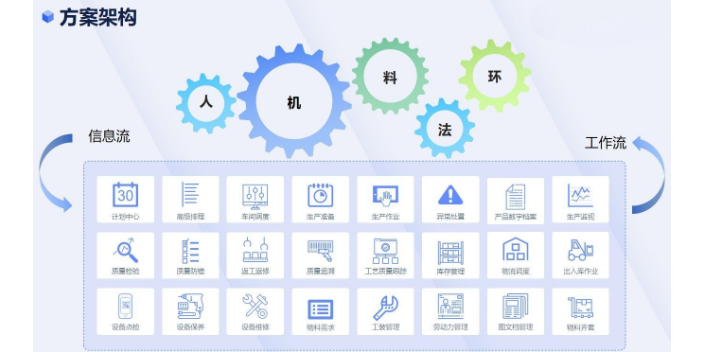
MES主要能够帮助制造企业解决如何生产的问题,例如,帮助企业提高设备利用率、降低交货周期、实现质量保障与追溯等目标。具体而言,如下图所示,MES的主要功能包括生产运营管理、产品质量管理、生产实时管控、生产动态调度等,对生产现场的“人、机、料、法、环、测”均实现了有效管理,紧扣质量管理理论中的六要素。,MES作为一个重要的生产过程管理与监控者,承接了上层管理系统和下层执行系统的集成。在数据越来越重要的如今,起着极其关键的作用。
MOM(ManufacturingOperationsManagement)是制造运营管理系统,通过协调管理企业的人员、设备、物料和能源等资源,把原材料或零件转化为产品的活动。MOM是一种由多种软件构成的制造管理集成平台。MOM的提出是2000年,比工业4.0、智能制造等新概念早了近十年之久,2003年,MOM正式进入国际标准。MOM覆盖的范围更广、更明确。MES涉及的范围,会根据针对的后续行业、软件系统的设计理念、功能模块等因素而各有不同,没有明确界限。而MOM可实现对整个制造运行过程中一切活动的管理。MES被视为针对MOM的一种具体实现方式,或是一种为解决某一类MOM问题而设计开发的软件产品。换句话来说,之前需要MES、WMS、QMS等多个IT系统来满足制造企业的业务需求,现在只需要一个MOM系统就可以搞定。基于此,MOM与MES形成一种兼容与包含的关系。江苏电梯电缆行业软件系统供应商众和昊天。
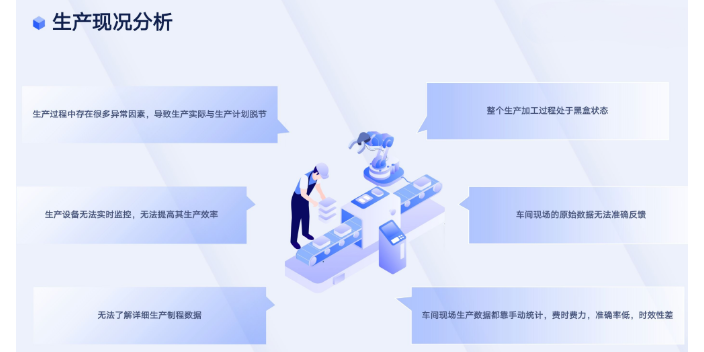
MES系统:俗称制造系统的大脑,整个车间的业务逻辑都要经过它的控制和记录,比如:工艺顺序、过程流追踪等,生产流程中90%以上的RawData都会首先存在MES。工厂里面80%+的人每天都要用到系统,其中80%+的人每天都要用到MES。EAP系统:设备自动化控制,主要负责给机台下指令和采集机台上的参数,分两类,一类是工艺特性参数,比如工件厚度和宽度等;一类是加工特性参数,比如功率、电流、角速度等。PS:a.并不是所有的参数都可以自动化采集,不能自动化采集的就在MES提供界面,手Key或者扫描进系统;b.EAP系统要给上位系统喂数据,比如MES、RMS和FDC。RMS:菜单/配方管理系统,主要用于卡控工艺特性参数,比如上料确认机台内的菜单设置是否在SOP规范内,超出就不允许Run货。FDC:故障侦测系统,主要用于卡控加工特性参数,比如工件和靶材距离持续变大,到一定值时候,就要更换靶材。四川精益咨询+软件系统服务商众和昊天科技有限公司。江苏设备联网系统品牌
四川农机行业MOM系统软件供应商众和昊天。常州机加工系统哪家不错
工厂因其生产的产品不同,有不同类型,大体上,可以分为流程型、离散型、单件生产,虽然跨类型的工厂差异非常大,但是基本活动是一致的,就是:搬运、加工、储存、检查这四个,如果再加上不得不的对物料状态的区分,还可以加上“收料”和“发货”,基本上是这六大类事务。此外就是一些预处理的辅助活动。这些生产活动某种程度看是通用的,与行业无关。离散制造介于流程制造和单件制造之间,兼具二者的的许多特性,可以以其为学习对象深入研究。制造主要活动可以被定义为搬运、加工、存储和检查这四个,其中很复杂的是加工,抛开工艺差异性,可以概括为是料号的跳转,它的特异性体现在对某个特意。针对工站和辅助活动的再细分才和具体行业以及工序息息相关。所以,理论上,MES系统在某个粒度界限之上实现通用,似乎是可行的,只是,如果再要细化时就要进行客制化开发了。常州机加工系统哪家不错
上一篇: 机加工软件公司
下一篇: 重庆IOT系统操作流程