南通磨床主轴厂家
电主轴离不开一些重要的附件:一套完整的精密电主轴系统除包括主轴本身外,高频变频装置、油雾润滑器、冷却装置、内置脉冲编码器、换刀装置等相关附件也很关键:高频变频装置:要提升加工速度,必须保证电主轴的高速旋转,从而带动切削工具高速运转。需要有一台设备来作为电主轴内置高速电动机的驱动装置,使其转速达到每分钟几万甚至是十几万次,高频变频装置的作用即在于此。为完成目标,高频变频器的输出频率必须要达到几千赫兹以上。电主轴内的各个零部件联系非常紧密,若其中有一个损坏,将会影响整个电主轴的运行。南通磨床主轴厂家
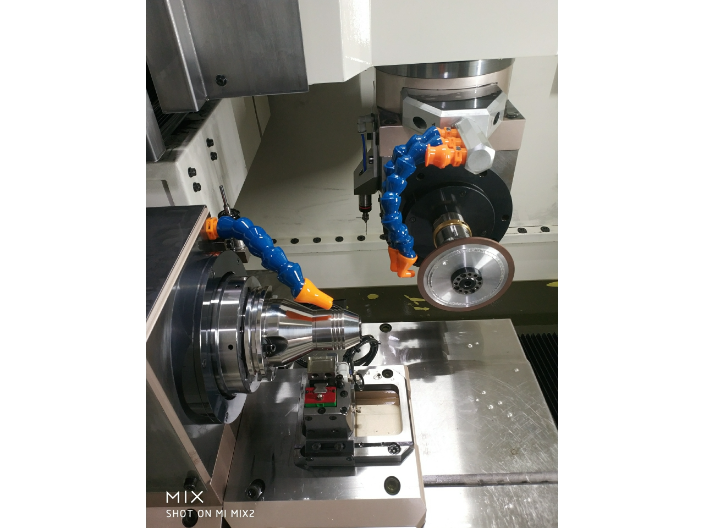
电主轴的位置偏移现象解析:经在故障出现后对加工中心进行了仔细观察,才发现故障的真正原因是精密电主轴在定向后发生位置偏移,奇怪的是主轴在定向后如用手碰一下主轴会产生向相反方向偏移,检查电气部分无任何报警,机械部分又很简单。该加工中心的定向使用编码器,所以从故障的现象和可能发生的部位来看,电气部分的可能性比较小,机械上主要的是联接。所以决定检查机械联接部分,在检查到编码器的联接时发现编码器上联接套的紧定螺钉松动,使联接套后退造成与精密电主轴的联接部分间隙过大使旋转不同步。任何产品在使用过程中都不可能一帆风顺,只有多了解一些处理措施才能在今后的使用带来帮助。石家庄SAACKE电主轴厂家电主轴主要用途:数控机床、机电设备、微型电机、压力转子。
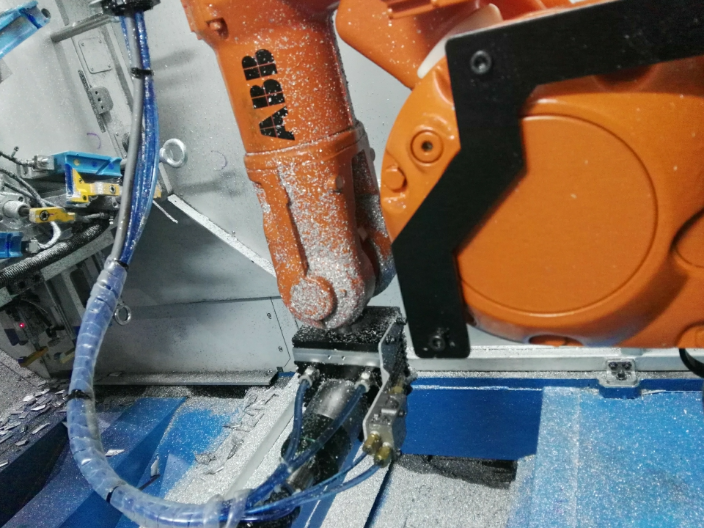
电主轴在模具切削加工中的优势:1.提高生产效率:高速电主轴具有高转速和大扭矩的特点,较高转速可达100,000RPM,能加工出非常精密、光洁的零件,省去其他等工序,很大程度提高生产效率。2.提高加工质量:硬切削加工较后成型表面,提高表面质量、形状精度(不只表面粗糙度低,而且表面光亮度高),用于复杂曲面的模具加工更具优势。3.模具不易变形:在高速切削时,大部分的切削热就被工件切削的飞屑带走,工件基本保持冷态,因而特别适合于容易生产热变形的零件。4.简化模具加工工序:对于各种难以加工的材料,实现高速切削加工,可以得到非常高的表面质量,减少甚至免除了火花放电及人工抛光程序,极大地简化了模具的加工过程。
电主轴常见故障与解决措施:轴承连续烧损,原因分析,润滑不好,转速过高,预加载荷过小或过大,承受载荷过大。解决措施,更换油脂或检查油雾质量,检查油道供油情况,测量转速,调整变频器保证电主轴的正常运转,检测并调整预加载荷,使其达到较佳值。主轴发热,原因分析,冷却水路不通畅,选用轴承精度较低,配合过紧,轴承反装或安装不到位,预加载荷太大,电源电压偏高,磨削进刀量过大。处理方法,检查并疏通水路,筛选较好的轴承,测量其尺寸,重新进行选配,适当减少预紧力,重新装配,检查定子和转子之间的气隙及电流值,检查供电电压,控制磨削进给量。由于当前电主轴主要采用的是交流高频电动机,故也称为“高频主轴”。
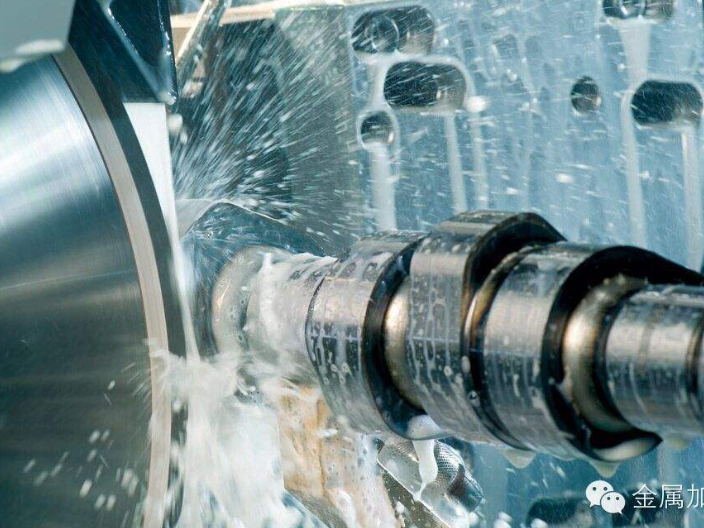
电主轴维护及使用注意事项?各个主轴通气后可达到密封状态,密封气流量请参考主轴外壳标签上的参数(必须严格控制密封气气压)。气压过大会破坏轴承的润滑脂或润滑系统,轴承失去润滑,主轴高速状态下轴承会损坏;气压过小则达不到密封作用。主轴后端的换刀气压请参考主轴外壳上标签上参数,当换刀气压大于主轴外壳标签上参数时,气体会通过中间拉杆从前端转子锥面和夹头的贴合面、夹头缝隙吹出,起到清洁锥面的作用。特别是陶瓷插芯研磨的工艺,必须定期对锥面做清洁工作。电主轴的矢量控制技术模仿直流电动机的控制。成都高速电主轴价格
电主轴具有高转速和大扭矩的特点,能加工出非常精密光洁的零件省去其他等工序,很大程度提高生产效率。南通磨床主轴厂家
电主轴通常采用动静压轴承、复合陶瓷轴承或电磁悬浮轴承。动静压轴承具有很高的刚度和阻尼,能大幅度提高加工效率、加工质量、延长刀具寿命、降低加工成本,这种轴承寿命多半无限长。复合陶瓷轴承在电主轴单元中应用较多,这种轴承滚动体使用热压Si3N4陶瓷球,轴承套圈仍为钢圈,标准化程度高,对机床结构改动小,易于维护。电磁悬浮轴承高速性能好,精度高,容易实现诊断和在线监控,但是由于电磁测控系统复杂,这种轴承价格十分昂贵,而且长期居高不下,没有得到普遍应用。南通磨床主轴厂家
上海天斯甲精密机械有限公司专注技术创新和产品研发,发展规模团队不断壮大。目前我公司在职员工以90后为主,是一个有活力有能力有创新精神的团队。公司业务范围主要包括:电主轴维修,电主轴,进口电主轴,磨削电主轴等。公司奉行顾客至上、质量为本的经营宗旨,深受客户好评。公司力求给客户提供全数良好服务,我们相信诚实正直、开拓进取地为公司发展做正确的事情,将为公司和个人带来共同的利益和进步。经过几年的发展,已成为电主轴维修,电主轴,进口电主轴,磨削电主轴行业出名企业。
上一篇: 精密主轴
下一篇: 石家庄永磁主轴供应商