珠海多机一体模温机哪里有
模温机对模具热疲劳的影响:在注塑过程中,模具需要承受高温高压,这会使模具产生热疲劳。热疲劳会导致模具出现微裂纹和疲劳失效等问题,缩短模具的使用寿命。模温机可以通过控制模具的温度波动和加热速度来降低模具的热疲劳。在加热和冷却过程中,模温机可以快速将模具加热到适宜的温度,并保持恒定的温度波动范围,避免模具出现急剧的温度变化,从而减少热应力和热疲劳。此外,模温机可以通过优化加热功率和冷却水流量等参数,实现能源的节约和优化利用,减少生产过程中的能源消耗,降低生产成本。模温机能满足各种不同的生产需求。珠海多机一体模温机哪里有
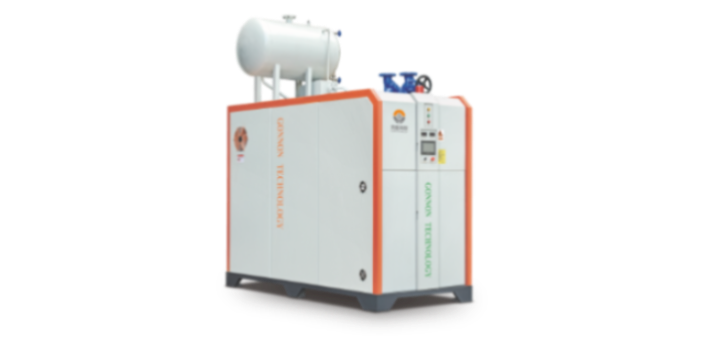
定期维护保养预防性维护和保养为了预防模温机出现故障,应定期进行预防性维护和保养。例如,每季度需要检查一次加热器、散热器、水泵等关键部件,确保其正常运转。此外,每半年需要清洗一次冷却水箱,以防止水垢等杂质的沉积。全部检查和维护为了确保模温机的长期使用,需要定期进行全部检查和维护。包括检查温度传感器、压力传感器等传感器的准确性和灵敏度,检查电气控制系统、安全保护装置等是否可靠、有效,检查润滑系统、液压系统等是否正常运行。苏州运油式模温机生产厂家模温机能提高企业的经济效益。
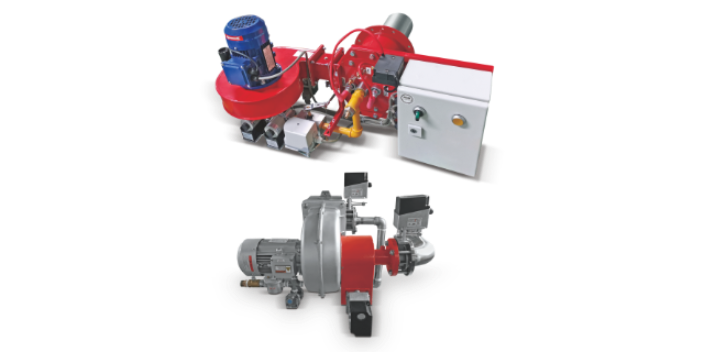
模温机的功能和参数显示:曲线分析:模温机支持曲线分析功能,用户可以在操作界面上查看模具温度随时间变化的曲线图。通过曲线图,用户可以对加热和冷却过程进行分析和优化,提高生产效率和产品质量。数据存储:模温机可以将加热和冷却过程中的数据记录下来,并保存在机器内置的存储器中。用户可以在操作界面上查看、分析和导出这些数据,以便对生产过程进行更好的监控和管理。在使用模温机时,需要注意以下事项:安全提示:操作模温机前,务必仔细阅读使用说明书,并遵守相关安全规定。特别是在设备维修或更换部件时,务必切断电源并确保机器完全停止运转。
模温机的温度控制:模温机的温度控制是实现模具温度精确控制的关键。模温机的温度控制主要包括以下几个方面:1.温度传感器:模温机中常用的温度传感器有热电偶和热敏电阻两种。它们可以实时监测模具的温度,并将温度信息反馈给控制器。2.控制器:模温机的控制器可以根据温度传感器的反馈信息,对加热器和冷却水的温度进行精确控制。控制器可以根据实际情况进行调整,以实现对模具温度的精确控制。3.模具温度分布:模具温度分布是影响塑料加工质量的重要因素。在模温机的温度控制过程中,需要考虑模具温度分布的均匀性,以确保塑料加工质量的稳定性。4.温度曲线记录:模温机的控制器可以记录温度曲线,以便后续进行分析和调整。温度曲线记录可以帮助工程师了解模具温度变化的规律,从而优化模具设计和加工工艺。模温机可根据不同工艺需求进行定制化设计。
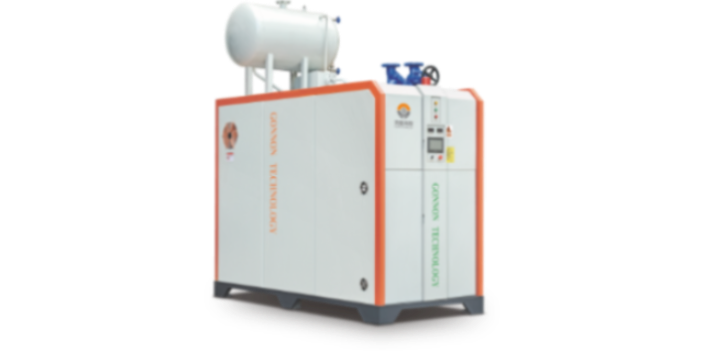
模温机在塑料薄膜制备中的应用:1.提高塑料薄膜的透明度在塑料薄膜制备过程中,模温机可以通过提高模具的温度,使得塑料材料能够更加均匀的熔化和流动,从而提高薄膜的透明度和光泽度。2.减少塑料薄膜的缩水率在塑料薄膜制备过程中,由于塑料材料的熔化和冷却过程,往往会导致薄膜的缩水率过大。而通过控制模温机的温度,可以使得薄膜的冷却速度更加均匀,从而减少薄膜的缩水率,提高薄膜的尺寸稳定性。3.提高塑料薄膜的韧性和耐热性在塑料薄膜制备过程中,模温机可以通过控制模具的温度,使得塑料材料更加均匀的熔化和流动,从而提高薄膜的韧性和耐热性。同时,模温机可以通过控制模具的冷却速度,使得薄膜的结晶度更加均匀,从而提高薄膜的韧性和耐热性。4.提高塑料薄膜的生产效率在塑料薄膜制备过程中,模温机可以通过控制模具的温度和冷却速度,使得塑料材料更加均匀的熔化和流动,从而提高生产效率。同时,模温机可以通过控制模具的温度和冷却速度,使得薄膜的尺寸稳定性更高,从而减少薄膜的废品率,提高生产效率。模温机能提高产品的冷却速度和定型效果。武汉燃气型模温机厂家
模温机适用于各种不同的成型工艺。珠海多机一体模温机哪里有
为了提高模温机的工作效率,可以采取以下措施:优化设计,提高设备的加热速度和冷却效率;合理选型依据,根据实际生产需要选择合适的模温机型号;加强日常维护管理,定期检查设备的运行状况和保养情况;推广智能化技术,运用物联网和大数据分析等手段实现设备的准确控制和优化运行;加强操作培训,提高设备操作人员的专业水平和规范意识。结论这里通过对模温机工作效率的评估指标、评估方法、影响因素和提高措施等方面的分析,明确了评估模温机工作效率的意义和价值。通过了解模温机的工作效率,企业可以更好地掌握生产过程的瓶颈,采取有效措施提高生产效率和产品质量。这对于企业的成本控制和长期发展具有重要意义。在实际操作过程中,企业应根据自身实际情况,制定合理的评估标准和操作规范,以确保模温机的高效运行。珠海多机一体模温机哪里有
上一篇: 郑州自动模温机价格
下一篇: 沈阳双油泵模温机哪家好