气冷真空硬化淬火工艺
渗硼和渗金属,渗硼可以是固体渗硼、液体渗硼和膏剂渗硼等,应用较多的是固体渗硼,市场上已有固体渗硼剂供应。固体渗硼后,表层的硬度高达1400-2800HV,耐磨性高,耐腐蚀性和抗氧化性能都较好。渗硼工艺常用于各种冷作模具上,由于耐磨性的提高,模具寿命可提高数倍或十余倍。采用中碳钢渗硼有时可取代高合金钢制作模具。渗硼也可应用于热作模具,如热挤压模等。渗硼层较脆,扩散层比较薄,对渗层的支撑力弱,为此,可采用硼氮共渗或硼碳氮共渗,以加强过渡区,使其硬度变化平缓。为改善渗硼层脆性,可采用硼钒、硼铝共渗。渗金属包括渗铬、渗钒、渗钛等工艺,均可用于处理冷作和热作模具,其中TD法(熔盐渗金属)已得到一些应用,可使模具寿命提高几倍乃至十几倍。真空淬火处理过程中使用.巴氮气或氩气,保证零件在无氧环境下进行加热。气冷真空硬化淬火工艺
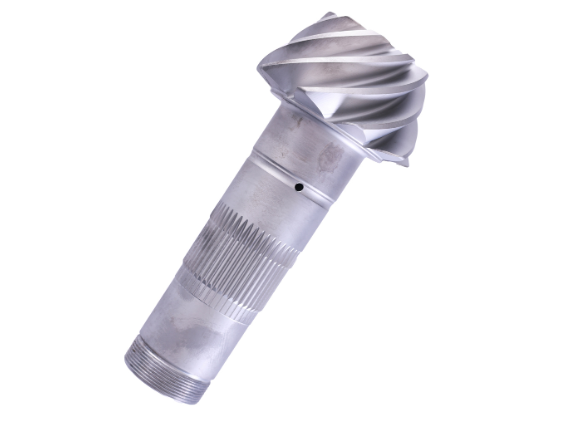
同炉淬火刀具的红硬度不同,经正常温度回火后,真空炉淬火刀具硬度均匀性好,偏差1.5HRC大约590~6000。℃回火后硬度偏差加大。用法国爱和公司EM由钴高速钢制成M3.同炉淬火550以下规格的丝锥℃回火三次后,硬度为65.7~66.8HRC(见图1)均匀性好。6000℃×2h回火后,硬度不均匀(见图2)。图1 1210℃淬火,550℃回火三次,图2 1210℃淬火,550℃回火两次 660℃回火1次,从图2可以看出,高温回火后,硬度约为62~63%HRC,20%在65~66HRC,其余70%为63~65HRC。600℃回火后硬度散差增加说明红硬度不同。浙江单介质真空硬化淬火参考价淬火可以大幅提高钢的刚性、硬度、耐磨性、疲劳强度以及韧性等。
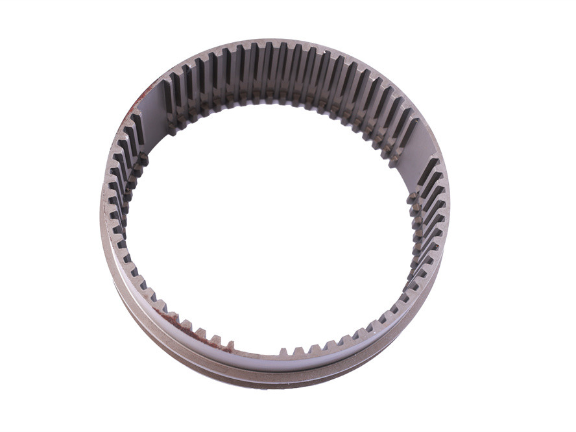
40Cr钢是一种中碳调制刚,价格适中,加工也比较容易,通过热处理,可以达到一定的耐磨性、韧性和塑性,该刚在550-570摄氏度之间时,具有较佳的综合的力学性能,适合高频淬火等表面硬化处理,且在生活中应用普遍,深受欢迎。40Cr钢热处理传统工艺概述,热处理工艺大体可分为整体、表面和化学热处理三种,根据40Cr钢的加热介质、温度和冷却法的不同,可采用不同的热处理工艺,获得不同的性能,获得需要的金相组织,以获得需要的力学性能。
渗碳后的几种热处理方法,渗碳只能改变零件表面的化学成分,要使零件获得外硬内韧的性能,渗碳热处理后还必须进行淬火加低温回火,来改善钢的强韧性和稳定零件的尺寸。根据工件的成分、形状和力学性能等,渗碳后常采用以下几种热处理方法。直接淬火+低温回火,将零件自热处理炉中取出直接淬火,然后回火以获得表面所需的硬度。直接淬火的条件有两点:渗碳热处理后奥氏体晶粒度在5-6级以上;渗碳层中无明显的网状和块状碳化物。20CrMnTi等钢在渗碳后大多采用直接淬火。真空高压气冷淬火的用途是材料的淬火和回火,不锈钢和特殊合金的固溶、时效,离子渗碳和碳氮共渗。
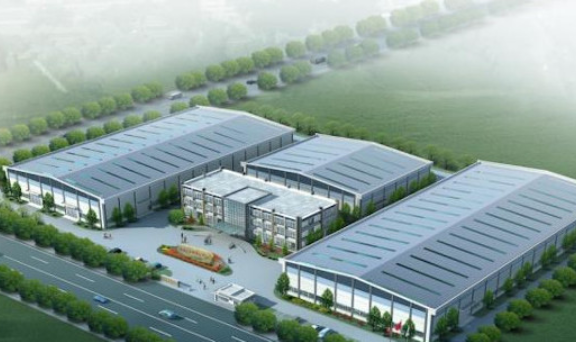
模具的真空退火,模具(模块)的真空退火易实现无氧化、无脱碳的热处理,有利于提高模具表面质量和生产效率,缩短工艺周期,模具表面可达到光亮,显微组织均匀一致。普通真空退火工艺是H13(4Cr5MoSiV1)钢模块普通真空退火工艺。模具退火采用真空炉(如WZT系列单室真空炉,极限真空度0.1Pa),将模块以60℃/h的速度缓慢加热到870℃,视模块有效尺寸决定保持时间(2~4h),也可以待到温后保持0.8min/mm。保温阶段压力控制在0.1~10Pa。冷却时可在真空状态下进行炉冷,当温度低于500℃时,可充入1×105Pa的高纯度N2或高纯度N2与其他还原性气体(如H2)的混合气进行冷却,以确保模块表面无氧化、不着色。经退火后的模块硬度<235HBW,组织为珠光体+均匀分布的粒状碳化物。热处理的工艺技术不断发展更新,发展至今,出现了真空热处理,可控气氛热处理和形变热处理等。苏州直接中性淬火哪家好
不锈钢中性淬火提高了其抗腐蚀性和机械性能,延长了使用寿命。气冷真空硬化淬火工艺
气相沉积,气相沉积按形成的基本原理,分为物理的气相沉积(PVD)和化学气相沉积(CVD)。PVD分为真空蒸镀、溅射镀和离子镀。离子镀是蒸镀和溅射镀相结合的技术,离子镀膜具有粘着力强、均镀能力好、被镀基体材料和镀层材料可以普遍搭配等优点,因而获得较普遍的应用。近年来,多弧离子镀受到人们的重视。目前,在模具上应用较多的是离子镀TiN,这种膜不仅硬度高,而且膜的韧性好、结合力强、耐高温。在TiN基础上发展起来的多元膜,如(TiAl)N、(TiCr)N等,性能优于TiN,是一类更有前途的新型薄膜。CVD是用化学方法使反应气体在基础材料表面发生化学反应形成覆盖层(TiC、TiN)的方法。CVD有多种方法。气冷真空硬化淬火工艺
上一篇: 风冷中性淬火价位
下一篇: 苏州乙炔低压渗碳过程