上海金属棒材金相检验
金属物理性能检测是一种测试和评估金属材料物理特性的过程。这些特性包括金属的机械性能、热性能、电性能、磁性能、化学性能等。金属物理性能检测是工业生产和科学研究中非常重要的一项工作,它可以帮助人们了解金属材料的性能和特点,为金属材料的选择、设计和制造提供科学依据。金属物理性能检测的方法包括金属拉伸试验、冲击试验、硬度测试、磁性测试、热处理试验等。这些测试方法可以通过专业的实验室设备进行,例如拉伸试验机、冲击试验机、硬度计、磁性测试仪和热处理设备等。这些设备可以对金属材料进行多种性能测试,从而得出金属材料的物理性能指标。金相检验服务的重要性是什么?上海金属棒材金相检验
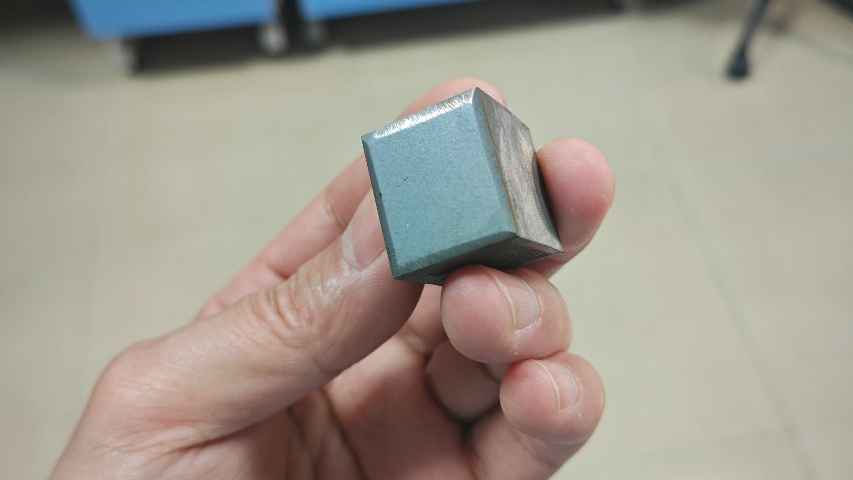
如何对金属进行表面处理,以便进行金相检验?对金属进行表面处理是为了去除表面杂质和氧化物,使得金相检验时能够更好地观察和分析金属的内部结构和组织情况。以下是几种常见的金属表面处理方法:1、机械抛光:采用磨料和磨料剂对金属表面进行切削和磨光处理,以去除氧化皮、毛刺等缺陷,使得金属表面光洁度提高,适用于硬度较高且非常规形状的金属。2、化学处理:将金属浸泡在酸、碱溶液中,去除表面氧化物、锈蚀物和污垢等杂质,使得金属表面变得干净光滑,适用于软性材料和大面积的金属。3、电解抛光:将金属表面置于电解液中,通过电解反应去除表面氧化物和杂质,使得金属表面光亮平滑,适用于需要高精度、高光洁度和高反光性的金属。上海金属棒材金相检验金属金相检验是通过对金属材料微观结构的分析和评估,来确认材料的质量、结构和性能的一种方法。
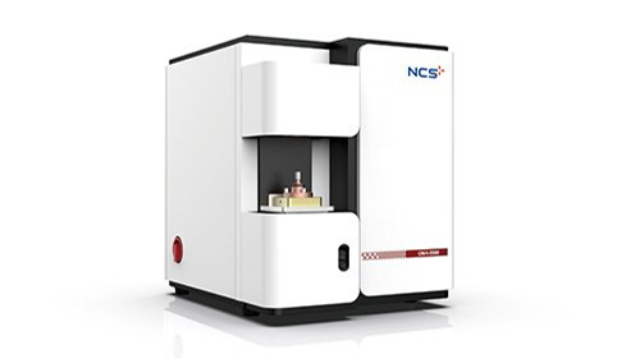
金属低倍组织检验中,材料的相组成会对材料性能产生影响吗?确定金属材料的相组成对于揭示材料的性能和特性非常重要。金属材料性质与其组织特征密切相关,材料的相组成是材料组织特征之一。相是指材料中互相分离出来的各个物质的组成部分。相组成的变化,可以直接或间接地对材料的性能产生影响,例如硬度、强度、延展性、韧性和热稳定性等。例如,在钢中,沙氏体的含量过高会使材料变脆,热处理时需要以较缓慢的加热、冷却速度进行;而珠光体含量适中的钢的强度和硬度较高,但韧性则较差。因此,通过金属低倍组织检验,可以研究材料的相组成和分布规律,进而对材料的性能进行评估和优化,通过制定相应的控制措施,提高材料的质量和性能。
金属金相检验是一种针对金属材料显微组织进行的测试和分析,旨在判断不同材料的显微组织及其异常,以便评估其性能和质量。这些测试可以帮助制造商和用户更好地了解金属材料的性能和质量,以便选择适合他们需求的材料。金属金相检验通常在以下情况下进行:新材料的质量控制、生产过程中的质量控制、材料失效的分析、材料的性能测试等等。金属金相检验的意义在于帮助制造商和用户更好地了解金属材料的性能和质量,以便选择适合他们需求的材料。此外,金属金相检验还可以帮助制造商改进生产工艺和产品设计,以提高产品质量和性能。金相拉伸试验通过施加拉力来评估金属材料的延展性、断裂强度和塑性变形能力。
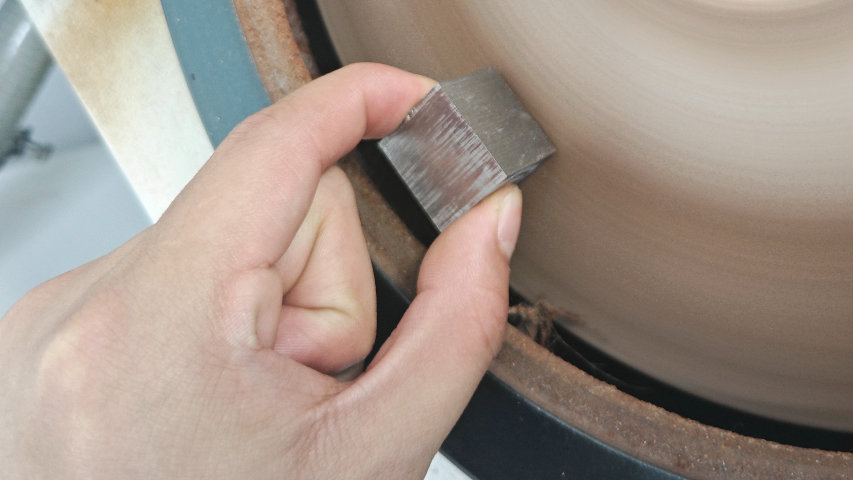
金属低倍组织检验中的组织特征有哪些?1、显微结构:金属材料的显微结构是指其晶粒的大小、形状、排列方式等。不同的金属材料具有不同的显微结构,如铸铁的石墨球状组织、钢的铁素体和贝氏体组织等。2、晶粒大小:晶粒大小是指金属材料中晶粒的尺寸。晶粒大小对金属材料的力学性能、耐腐蚀性能等有很大影响。3、晶粒形状:晶粒形状是指金属材料中晶粒的形状,如立方体、六角形等。晶粒形状也会影响金属材料的性能。4、晶粒排列方式:晶粒排列方式是指金属材料中晶粒的排列方式,如单向排列、交错排列等。晶粒排列方式也会影响金属材料的性能。5、相组成:金属材料中的相是指具有相同化学成分和结构的晶体区域。不同的相具有不同的性质和组织结构,如铁素体、贝氏体、马氏体等。金相拉伸试验是评估金属材料力学性能的常见测试方法。郑州金属型材低倍组织检验
金相检验的步骤主要包括试样制备、试样磨削、试样腐蚀、试样清洗、试样显微镜观察等。上海金属棒材金相检验
金属物理性能检测是指对金属材料进行各种物理性能测试的过程,以确定其力学、热学、电学、磁学等方面的性能指标。这些测试可以帮助人们了解金属材料的特性和性能,为其在工程领域的应用提供基础数据和参考依据。在金属金相检验中,不同材料的显微组织及其异常可以通过显微镜观察和分析来判断。该过程涉及到样品的制备、显微镜观察、图像分析等步骤。首先,需要将样品制成薄片,并进行腐蚀处理,以便观察其内部组织。随后,通过显微镜观察样品的组织结构、晶粒大小、晶界分布等特征,以判断其材料类型、加工工艺、热处理状态等信息。如果存在异常,如裂纹、气孔、夹杂物等,则需要进一步分析其原因和对材料性能的影响。通过金属金相检验,可以为材料的选择、设计和生产提供重要的参考和指导。上海金属棒材金相检验
上一篇: 湖州金属管材低倍组织检验服务厂家
下一篇: 金属管材高倍组织检验售价