深圳不锈钢电解抛光工艺
不锈钢电解抛光可以提高接头的耐腐蚀性能。不锈钢本身具有良好的耐腐蚀性能,但焊接接头处容易形成焊渣、氧化物等缺陷,从而降低了接头的耐腐蚀性能。通过电解抛光,可以去除这些缺陷,提高接头的表面光洁度和耐腐蚀性能,延长接头的使用寿命。此外,不锈钢电解抛光还可以改善接头的机械性能。焊接接头处常常存在焊缝、气孔等缺陷,这些缺陷会降低接头的强度和韧性。通过电解抛光,可以去除这些缺陷,提高接头的表面平整度和机械性能,增强接头的承载能力和抗拉强度。不锈钢电解抛光还可以提高接头的美观度。焊接接头处常常存在焊瘤、焊渣等不平整的表面,影响了接头的外观质量。通过电解抛光,可以使接头表面更加光滑、亮丽,提高接头的美观度,满足不同应用场景对外观要求的需求。不锈钢电解抛光过程中,电流密度、电解液温度和抛光时间等参数的控制至关重要。深圳不锈钢电解抛光工艺
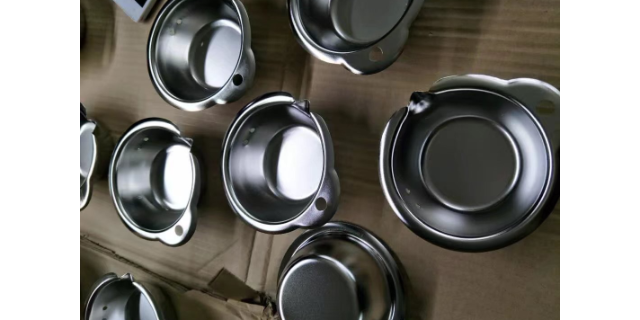
不锈钢电解的价值主要体现在提高耐腐蚀性能、增强材料硬度、提高亮度和整体美观度、去除表面污染物、定制化处理、环保可持续以及降低生产成本等方面。这些价值使得不锈钢电解技术在各个行业中得到了广泛的应用,并为企业创造了更多的商业机会和价值。不锈钢电解可以解决以下问题:表面质量:不锈钢电解能够提高不锈钢制品的表面质量,去除表面氧化膜、铁锈、污渍等表面缺陷,得到平整度高、无明显瑕疵和均匀光亮的表面。这有助于提高产品的美观度和性能表现。江门表面电解抛光厂家在市场竞争激烈的如今,不锈钢电解抛光技术为企业提供了独特的竞争优势和差异化卖点。
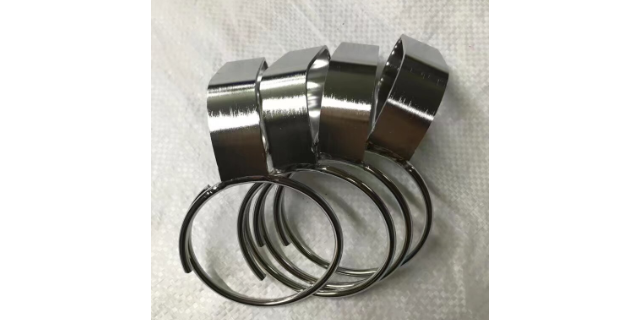
不锈钢电解抛光技术,以其独特的优势,在多个领域得到了比较大应用。在建筑行业中,不锈钢电解抛光可用于装饰材料的表面处理,使建筑外观更加光滑亮丽,提升整体的美观度。在医疗器械领域,电解抛光能够去除不锈钢表面的微小瑕疵,提高器械的洁净度和耐腐蚀性,从而保障患者的使用安全。此外,在汽车工业中,电解抛光技术同样发挥着比较大的作用,它可以使汽车零部件表面更加光滑,从而增强零件的耐磨性和耐腐蚀性,延长整体使用寿命。不锈钢电解抛光技术的应用场景非常多,不仅能提升了产品的外观质量,更增强了其性能和使用寿命。随着科技的不断进步,电解抛光技术将持续优化,为更多领域提供更加高效的表面处理解决方案,推动相关产业的可持续发展。
不锈钢电解抛光技术能够去除不锈钢表面的氧化物,形成一层致密的氧化膜,从而提高不锈钢的耐腐蚀性能。这使得船舶能够更好地抵御海水的侵蚀,延长其使用寿命。此外,不锈钢电解抛光技术还能够提高船舶的清洁度和卫生性能。船舶作为一种运输工具,其卫生状况对于乘客和船员的健康至关重要。不锈钢电解抛光技术能够去除不锈钢表面的污渍和细菌,使得船舶表面更加洁净、卫生。这有助于提高船舶的卫生状况,减少细菌滋生的可能性,保障乘客和船员的健康安全。综上所述,不锈钢电解抛光技术在船舶制造中具有广阔的应用前景。它能够提高船舶外观的美观度,增加其市场竞争力;提高船舶的耐腐蚀性能,延长其使用寿命;提高船舶的清洁度和卫生性能,保障乘客和船员的健康安全。随着船舶制造技术的不断进步,不锈钢电解抛光技术将会在船舶制造中发挥越来越重要的作用。不锈钢电解抛光是一种精密的表面处理工艺,需要精确控制抛光时间和电流密度等参数以确保效果。
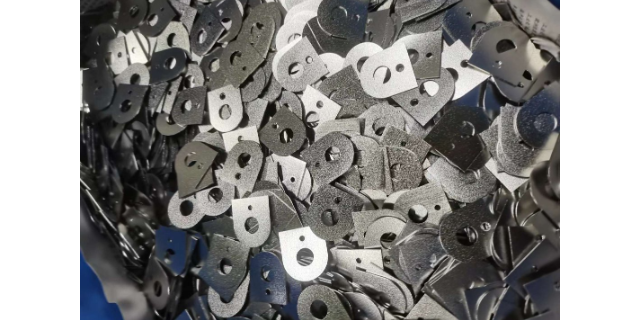
在电解抛光完成后,需要对不锈钢制品进行中和处理,以去除电解液残留和中和电解液的酸碱度。可以使用中和剂进行处理,同时进行冲洗,确保表面干净。将抛光完成的不锈钢制品进行清洗,去除中和剂和残留的电解液。可以使用清水进行冲洗,也可以使用酒精进行擦拭,确保表面干净。然后将制品进行干燥,可以通过自然风干或者烘干的方式进行。通过以上的工艺流程,不锈钢电解抛光可以提高不锈钢制品的光洁度和美观度。同时,还可以去除表面的氧化物和污染物,提高不锈钢制品的耐腐蚀性能。不锈钢电解抛光后表面的硬度和耐磨性得到显著提高,延长了产品的使用寿命。医疗器械电解抛光加工
不锈钢电解抛光技术的不断创新和发展,推动了其在各种领域的应用,满足了不断变化的市场需求。深圳不锈钢电解抛光工艺
不锈钢是一种常见的金属材料,具有耐腐蚀、耐高温和美观的特点。然而,不锈钢表面通常呈现出一种粗糙的外观,这在某些应用中可能不够理想。为了改善不锈钢的外观,人们常常使用抛光技术将其表面处理成镜面效果。抛光不锈钢表面以获得镜面效果需要经过清洁、磨平、选择合适的抛光材料和工具、均匀涂抹抛光材料、适当施加压力和速度、定期清洗抛光工具以及清洁和保护等步骤。抛光过程完成后,需要进行清洁和保护。使用清洁剂和清水将不锈钢表面彻底清洗,以去除抛光过程中产生的残留物。然后,可以使用不锈钢抛光剂或保护剂来增加不锈钢表面的光泽和耐腐蚀性能。这些产品可以形成一层保护膜,防止不锈钢表面再次受到污垢和腐蚀的侵害。深圳不锈钢电解抛光工艺
上一篇: 惠州303不锈钢电解抛光设备
下一篇: 深圳不锈电解抛光厂家