天津新材料半导体器件加工价格
干法刻蚀又分为三种:物理性刻蚀、化学性刻蚀、物理化学性刻蚀。其中物理性刻蚀又称为溅射刻蚀。很明显,该溅射刻蚀靠能量的轰击打出原子的过程和溅射非常相像。(想象一下,如果有一面很旧的土墙,用足球用力踢过去,可能就会有墙面的碎片从中剥离)这种极端的刻蚀方法方向性很强,可以做到各向异性刻蚀,但不能进行选择性刻蚀。化学性刻蚀利用等离子体中的化学活性原子团与被刻蚀材料发生化学反应,从而实现刻蚀目的。由于刻蚀的中心还是化学反应(只是不涉及溶液的气体状态),因此刻蚀的效果和湿法刻蚀有些相近,具有较好的选择性,但各向异性较差。悬浮区熔法加工工艺:先从上、下两轴用夹具精确地垂直固定棒状多晶锭。天津新材料半导体器件加工价格
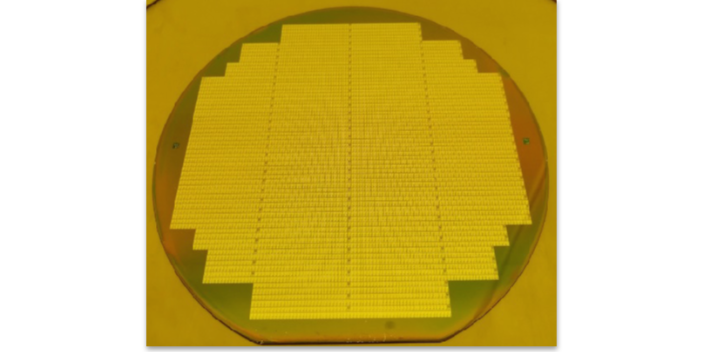
光刻机又名:掩模对准曝光机,曝光系统,光刻系统等,是制造芯片的中心装备。它采用类似照片冲印的技术,把掩膜版上的精细图形通过光线的曝光印制到硅片上。光刻胶是光刻工艺中较关键材料,国产替代需求紧迫。光刻工艺是指在光照作用下,借助光刻胶将掩膜版上的图形转移到基片上的技术,在半导体制造领域,随着集成电路线宽缩小、集成度大为提升,光刻工艺技术难度大幅提升,成为延续摩尔定律的关键技术之一。同时,器件和走线的复杂度和密集度大幅度提升,高级制程关键层次需要两次甚至多次曝光来实现。其中,光刻胶的质量和性能是影响集成电路性能、成品率及可靠性的关键因素。深圳压电半导体器件加工流程微机电系统是微电路和微机械按功能要求在芯片上的集成,尺寸通常在毫米或微米级。
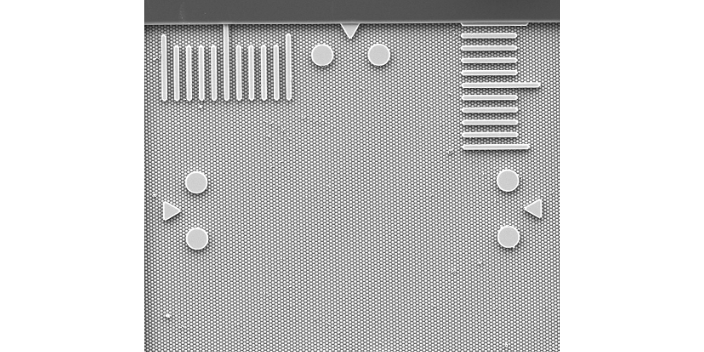
微纳加工技术是先进制造的重要组成部分,是衡量国家高级制造业水平的标志之一,具有多学科交叉性和制造要素极端性的特点,在推动科技进步、促进产业发展、拉动科技进步、保障**安全等方面都发挥着关键作用。微纳加工技术的基本手段包括微纳加工方法与材料科学方法两种。很显然,微纳加工技术与微电子工艺技术有密切关系。微纳加工大致可以分为“自上而下”和“自下而上”两类。“自上而下”是从宏观对象出发,以光刻工艺为基础,对材料或原料进行加工,较小结果尺寸和精度通常由光刻或刻蚀环节的分辨力决定。“自下而上”技术则是从微观世界出发,通过控制原子、分子和其他纳米对象的相互作用力将各种单元构建在一起,形成微纳结构与器件。
光刻工艺是半导体器件制造工艺中的一个重要步骤,该步骤利用曝光和显影在光刻胶层上刻画几何图形结构,然后通过刻蚀工艺将光掩模上的图形转移到所在衬底上。这里所说的衬底不只包含硅晶圆,还可以是其他金属层、介质层。光刻的优点是它可以精确地控制形成图形的形状、大小,此外它可以同时在整个芯片表面产生外形轮廓。不过,其主要缺点在于它必须在平面上使用,在不平的表面上它的效果要差一些。此外它还要求衬底具有极高的清洁条件。将单晶硅棒分段成切片设备可以处理的长度,切取试片测量单晶硅棒的电阻率含氧量。
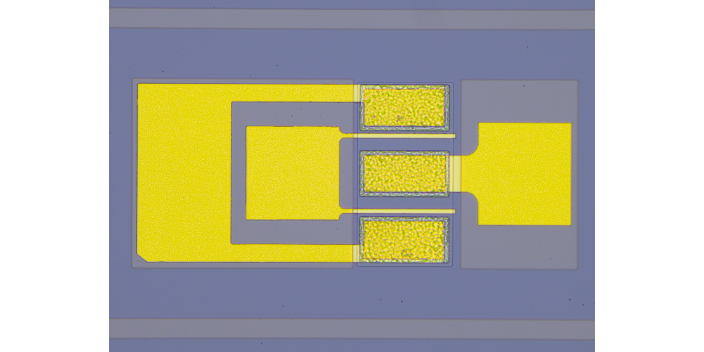
单晶硅是从大自然丰富的硅原料中提纯制造出多晶硅,再通过区熔或直拉法生产出区熔单晶或直拉单晶硅,进一步形成硅片、抛光片、外延片等。直拉法生长出的单晶硅,用在生产低功率的集成电路元件。而区熔法生长出的单晶硅则主要用在高功率的电子元件。直拉法加工工艺:加料→熔化→缩颈生长→放肩生长→等径生长→尾部生长,长完的晶棒被升至上炉室冷却一段时间后取出,即完成一次生长周期。悬浮区熔法加工工艺:先从上、下两轴用夹具精确地垂直固定棒状多晶锭。用电子轰击、高频感应或光学聚焦法将一段区域熔化,使液体靠表面张力支持而不坠落。移动样品或加热器使熔区移动。这种方法不用坩埚,能避免坩埚污染,因而可以制备很纯的单晶,也可采用此法进行区熔。半导体指常温下导电性能介于导体与绝缘体之间的材料。黑龙江生物芯片半导体器件加工
刻蚀先通过光刻将光刻胶进行光刻曝光处理,然后通过其它方式实现腐蚀处理掉所需除去的部分。天津新材料半导体器件加工价格
微流控技术是以微管道为网络连接微泵、微阀、微储液器、微电极、微检测元件等具有光、电和流体输送功能的元器件,较大限度地把采样、稀释、加试剂、反应、分离、检测等分析功能集成在芯片上的微全分析系统。目前,微流控芯片的大小约几个平方厘米,微管道宽度和深度(高度)为微米和亚微米级。微流控芯片的加工技术起源于半导体及集成电路芯片的微细加工,但它又不同于以硅材料二维和浅深度加工为主的集成电路芯片加工技术。近来,作为微流控芯片基础的芯片材料和加工技术的研究已受到许多发达国家的重视。天津新材料半导体器件加工价格
广东省科学院半导体研究所属于电子元器件的高新企业,技术力量雄厚。公司是一家****企业,以诚信务实的创业精神、专业的管理团队、踏实的职工队伍,努力为广大用户提供***的产品。公司业务涵盖微纳加工技术服务,真空镀膜技术服务,紫外光刻技术服务,材料刻蚀技术服务,价格合理,品质有保证,深受广大客户的欢迎。广东省半导体所以创造***产品及服务的理念,打造高指标的服务,引导行业的发展。
上一篇: 广东双靶磁控溅射特点
下一篇: 山西半导体器件加工报价