工业DCS控制系统怎么样
1987年至今,各厂家采用国际标准化组织(ISO)开放系统互连(OSI)结构基础上产生制造自动化协议(MAP)标准来解决不同机型的互连问题。 DCS系统在硬件上使用了更先进的CPU及冗余技术,存储容量及通讯速度大幅度提高,软件上采用通用操作系统。在该阶段DCS将控制、监督和管理调度有机结合起来,实现了各种生产经营信息的自动化管理。集散系统进入第三代,其技术特点表现为:1)采用开放系统管理;2)操作站采用32位微处理器;3)采用实时多用户多任务的操作系统。系统支持远程调试和优化,降低运维成本。工业DCS控制系统怎么样
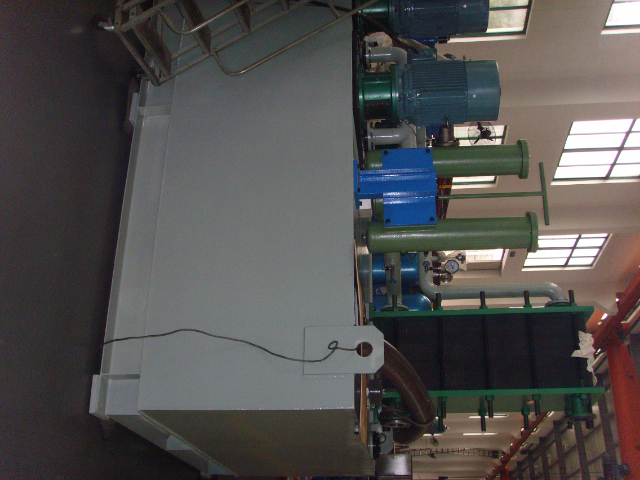
DCS系统发展趋势,DCS系统发展趋势之一是智能化,越来越多的DCS系统采用智能化技术,以改善系统的运行效率和稳定性,降低操作成本。DCS系统还在快速发展更加现代化的通信技术,让系统可以用更高效的方式进行网络通信,较大程度上提高系统的可靠性和可维护性。此外,DCS系统还将与更多的先进技术结合起来,比如互联网、大数据、人工智能等,使DCS系统的应用更加灵活。未来,DCS系统将会发展出更加智能、高效、可靠的特性,满足工业应用的更高要求。北京分布式DCS控制系统方案控制策略灵活多样,可针对不同生产过程进行定制。
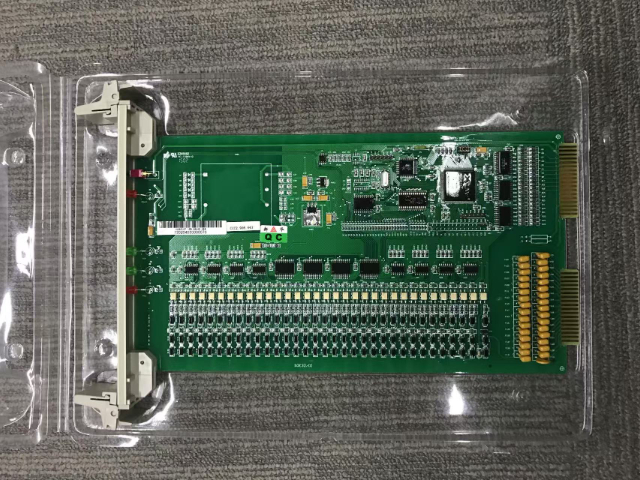
DCS系统架构,DCS系统具备以下特点:分散性: DCS系统将控制和监测功能分布在多个分散的控制器或计算机上,这使得系统更具灵活性和可扩展性。高可靠性: DCS系统通常采用冗余设计,即多个控制器互为备份,以提高系统的可靠性和容错性。实时性: DCS系统能够快速响应输入信号,实时监测和控制工业过程,确保过程的稳定性和安全性。网络化: DCS系统通过网络将各个控制单元连接在一起,实现数据的共享和传输,以及交互操作与系统管理。开放性: DCS系统通常支持开放的通信协议和接口,可以与其他系统进行集成,提供更强大的功能和扩展性。
当大量现场信息由智能仪表或通过现场总线直接进入计算机控制系统后,存在着计算机内部应用程序对现场信息的共享与交互问题。由于缺乏统一的连接标准,工控软件往往需要为硬件设备开发专门使用的驱动程序。这样一旦硬件设备升级换代,就需要对相应的驱动程序进行更改,增加了系统的维护成本。即使计算机中的SCADA有单独的驱动程序,但一般也不允许同时访问相同的设备,否则很容易造成系统崩溃。可见,现场控制层作为企业整个信息系统的底层部分,必然需要与过程管理层和经营决策层进行集成,这样也存在着监控计算机如何与其它计算机进行信息沟通和传递的问题。系统具备应急预案,如火灾、爆裂等紧急情况下的自动停机。
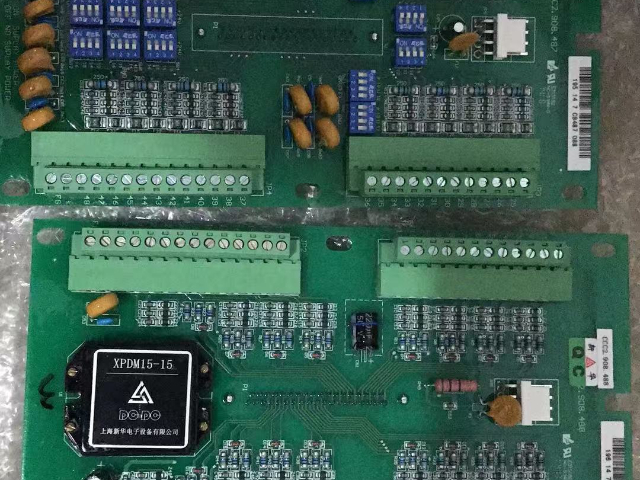
计算机集成技术和现场总线的发展,将对DCS的结构产生重大影响。目前DCS的结构将受到上下肢解,上层工作站将与CIPS紧密结合,DCS将演变成CIPS 的低层部分;在现场级,现场总线的应用将使传统的DCS I/O结构彻底改变。现场总线将对自控领域带来深刻影响,工业控制系统的体系结构将以统一的现场总线为纽带构成,现场控制系统(FCS)将是21世纪的开放控制系统。DCS系统是分散控制系统(Distributed Control System)的缩写,它是一种用于监控和控制工业过程的自动化系统。DCS控制系统的普及推动了智能制造的发展,为工业4.0的实现打下了基础。北京通用DCS控制系统行价
DCS控制系统能够支持过程优化与节能减排,符合现代产业发展的要求。工业DCS控制系统怎么样
由于控制系统往往是不同厂商开发的专门使用系统,相互之间兼容性差,与高层的商业管理软件之间又缺乏有效的通信接口,因此通信规范问题成为了制约控制系统突破“信息孤岛”的瓶颈。OPC(OLE for Process Control)的出现,建立了一套符合工业控制要求的通信接口规范,使控制软件可以高效、稳定地对硬件设备进行数据存取操作,应用软件之间也可以灵活地进行信息交互,极大提高了控制系统的互操作性和适应性。同样是传感器的采样,压力传感器的变化时间很短,我们可以用200ms的任务周期采样,而温度传感器的滞后时间很大,我们可以用2s的任务周期采样。这样,DCS可以合理的调度控制器的资源。工业DCS控制系统怎么样
上一篇: 深圳燃气PLC控制系统怎么样
下一篇: 北京国产DEH控制系统市场价格