茂名车间可视化管理系统
ESOP可视化看板在企业管理与决策支持方面发挥着重要作用。以下是其主要应用场景和优势:实时数据展示与监控,生产数据可视化:ESOP可视化看板通过电子显示屏将生产现场的各种信息实时呈现出来,如生产计划、产量、质量、设备状态等。这使得企业管理层能够迅速获取生产线的实时数据,掌握生产进度和效率。根据多个行业报告和实际应用案例,ESOP可视化看板在提升企业生产管理透明度方面得到了认可。异常报警与预警:当生产线出现异常情况(如设备故障、质量问题等)时,ESOP看板能够立即发出报警信号,并显示相关处理建议。这有助于企业快速响应并解决问题,减少生产中断时间和损失。实时性:ESOP看板的实时数据更新功能确保了管理层能够及时获取到关键信息,从而做出更加准确的决策。结合生产数据的实时采集和监控,企业可以分析生产过程中的瓶颈和问题,进而优化生产流程,提高生产效率。茂名车间可视化管理系统
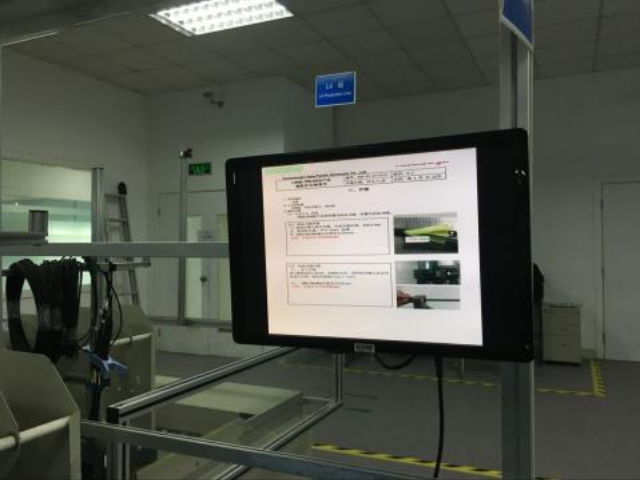
实时数据采集:生产看板通过与设备传感器和监控系统的连接,实时采集设备的运行状态、故障信息以及维护保养计划等数据。这些数据为设备管理和维修提供了便捷的方式,使得管理人员可以及时发现设备异常情况,并采取相应的措施。;数据整合与展示:生产看板可以整合ERP/MES系统数据,将复杂的数据以饼状图、柱状图等形式实时呈现,使得管理者能够快速了解生产情况。同时,通过丰富的可视化元素和图表类型,展示制造企业销售、财务、绩效、质量等不同业务主题的数据,为生产决策提供有力支持。汕尾工厂可视化管理开发通过数据分析,企业可以制定更合理的能源使用计划,实现能源的合理利用和节约,降低生产成本。
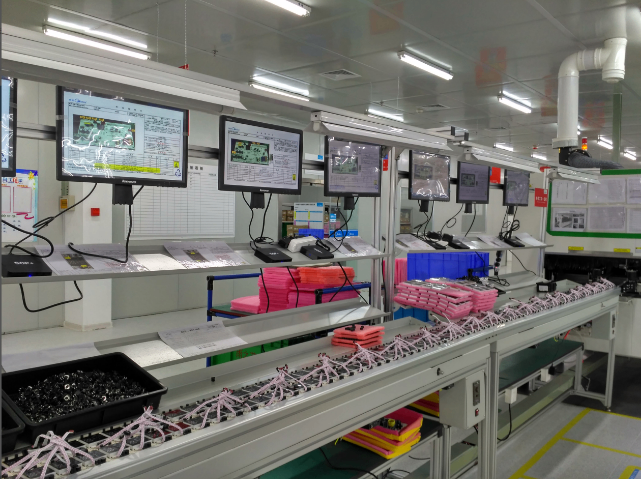
人员调度与绩效展示:生产看板可以展示工人的生产绩效、工时情况和奖励政策等信息。这鼓励员工积极工作,增强工作动力,提高整体生产效率;应用示例:在车间或生产线上,生产看板可以显示各个员工的生产数量、生产质量、工时等信息,以及相应的奖励政策,激励员工提高生产效率和质量;安全监测:生产看板可以实时展示安全监测信息,如安全隐患、安全违规记录等。这有助于加强安全意识,预防安全事故的发生;应用示例:在工厂的安全监测区域,生产看板可以显示安全巡检记录、安全隐患整改情况等信息,以便管理人员及时了解和解决安全问题;应用示例:在车间或生产线上,生产看板可以显示各个员工的生产数量、生产质量、工时等信息,以及相应的奖励政策,激励员工提高生产效率和质量。
ESOP在提升决策质量时,我们主要关注的是其作为电子化管理工具在信息管理、流程优化、实时监控等方面的优势,这些优势间接促进了决策质量的提升。以下是具体的分析:优化决策流程,标准化作业流程:ESOP系统通过制定和展示标准化的作业流程,减少了操作中的随意性和不确定性,为决策者提供了清晰的操作指南和决策依据。自动化数据分析:ESOP系统可以与数据分析工具结合,对生产数据进行自动化分析,提取关键指标和趋势,帮助决策者快速识别问题、评估风险并制定解决方案。可定义时间为当前的北京时间自动走时。
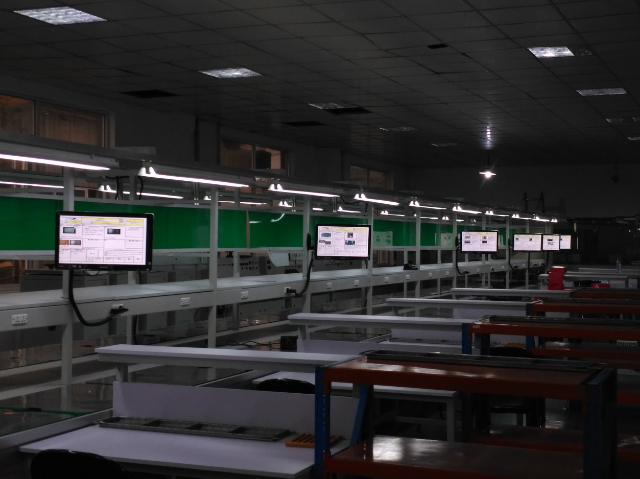
可视化系统可以与数字化工厂中的其他系统(如MES、ERP等)进行集成,实现数据的共享和协同工作;通过与其他系统的集成,ESOP系统可以获取生产数据和信息,提高实时监控的准确性和全面性;集成后的系统可以共同构建数字化工厂的完整生态,提升整个工厂的智能化水平;可视化系统是一个持续优化的过程,通过对实时监控数据的分析和反馈,系统可以不断进行自我优化和改进;用户可以根据实际需求对系统进行定制和扩展,满足不断变化的生产需求;通过持续优化和改进,可视化系统可以更好地服务于数字化工厂的生产管理,提高生产效率和质量。可跟ERP等管理系统无缝对接,自主上传报表。茂名仓库可视化管理软件
可将它们绑定到不同的工艺节点中。茂名车间可视化管理系统
深圳市昇航软件科技有限公司是广东天琴信息技术有限公司(股票代码:892273)控股子公司,深圳昇航致力于精益制造智能管理系统的研发和应用推广,可为制造企业提供SH-MES精益制造执行系统、WMS仓库管理系统、APS排程系统、E-SOP可视化看板系统、品质追溯系统等,力求能为制造企业快速部署智能信息化管理方案提供产品与解决方案,我们拥有方案制定专业团队、专业的软件研发团队和产品部署实施团队,帮助客户高效而精确的部署应用系统。 深圳昇航通过在精益制造领域的不断探索与创新,已形成业界的智能制造工厂软硬件一站式解决方案,产品方案广泛应用于3C电子、通讯电子、汽车电子、注塑冲压、机械加工、五金等各行业,业务范围遍布广国。凭借市场良好口碑,深圳昇航已与众多企业达成合作关系,其中包括信义玻璃、长虹电器、比亚迪、阿尔卑斯、上海逸航、北京地铁等企业,助力客户构建数字化与工业化相结合的智能制造工厂。茂名车间可视化管理系统