汕尾铝压铸PVD涂层制造商
常用的PVD涂层附着力评估方法:1.划格法:这是一种简单且常用的附着力测试方法。通过在涂层表面划制交叉的格子,然后用胶带粘贴并迅速撕下,观察格子内涂层的脱落情况来评估附着力。脱落越少,附着力越好。2.拉伸法:此方法使用专门的拉伸试验机,将涂层与基材之间的结合力拉伸至断裂,通过测量断裂时的拉力和涂层断裂的面积来计算附着力。3.冲击试验:利用重锤从一定高度自由落体,冲击涂层表面,观察涂层是否出现开裂、剥落等现象,以评估其抵抗冲击的能力。4.弯曲试验:将涂有PVD涂层的基材弯曲至一定角度,观察涂层在弯曲过程中是否出现开裂或剥落,以评估其在受力弯曲时的附着力。采用PVD涂层,可以减少机械零件的摩擦和能量损失。汕尾铝压铸PVD涂层制造商
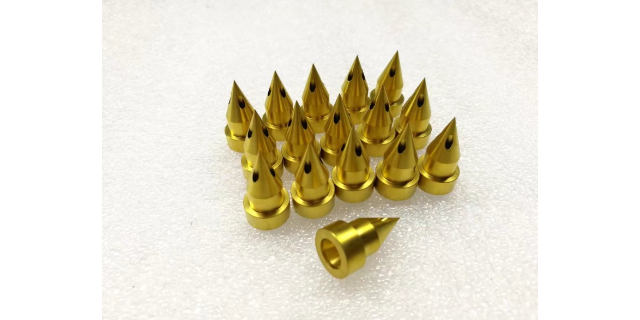
PVD涂层在提高材料光学性能方面的应用如何?PVD,即物理的气相沉积,是一种先进的表面处理技术。近年来,这一技术在提高材料光学性能方面展现出厉害的应用效果,成为光学领域的研究热点。这里将对PVD涂层在提高材料光学性能方面的应用进行深入探讨。PVD涂层技术简介PVD技术通过在真空条件下,利用物理方法将材料气化成原子、分子或离子,再沉积到基材表面形成薄膜。这种技术可以制备出具有高纯度、高密度、均匀性好且附着力强的薄膜,因此普遍应用于光学、电子、机械等领域。肇庆铝压铸PVD涂层生产厂家PVD涂层在电子设备中起到了良好的绝缘作用。
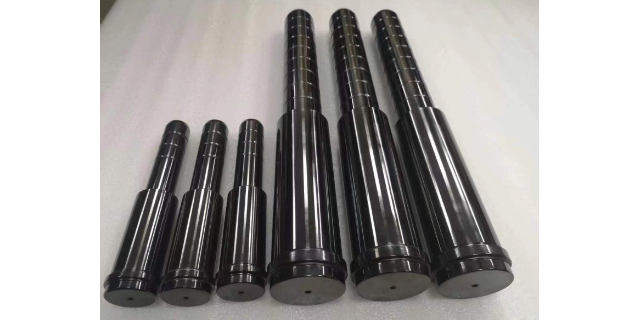
PVD涂层技术的特点:1.高纯度与高质量:由于PVD过程在真空环境中进行,避免了大气中的氧、氮、水等有害物质的污染,因此能够制备出高纯度和高质量的涂层。2.强结合力:PVD涂层与基体之间通过原子级别的结合,具有极强的附着力。3.普遍的材料选择:几乎所有固体材料都可以用作PVD涂层的材料源。4.环保与节能:相比化学气相沉积(CVD)等技术,PVD技术更加环保,且能源消耗较低。PVD涂层技术因其独特的优势,在刀具、模具、汽车零部件、航空航天、电子电器等多个领域得到了普遍应用。它能够明显提高工件表面的硬度、耐磨性、耐腐蚀性和装饰性,从而延长使用寿命,提升产品性能。总结PVD涂层技术以其高纯度、高质量、强结合力等特点,在现表示面工程领域中占据了重要地位。与CVD、电镀、喷涂等传统涂层技术相比,PVD技术在涂层质量、环保性能、材料选择等方面具有明显优势,是未来表面工程技术发展的重要方向之一。
PVD涂层技术的一个重要特点是其涂层的厚度可控性。通过精确控制涂层的厚度,可以在保证涂层性能的同时,较大限度地减少涂层对基体材料性能的影响。这对于一些对材料性能要求极高的应用,如高精度机械零件和航空航天组件,具有重要意义。然而,虽然PVD涂层在提高材料耐高温性能方面具有明显优势,但在实际应用中仍需考虑涂层的制备成本、工艺复杂性以及涂层与基体材料的结合力等问题。随着PVD技术的不断发展和进步,相信这些问题将得到有效解决,PVD涂层在提高材料耐高温性能方面的应用将更加普遍。综上所述,PVD涂层技术在提高材料耐高温性能方面发挥着重要作用。通过形成一层保护膜,阻隔高温环境与基体材料的直接接触,以及优化材料的热传导性能,PVD涂层明显提高了材料的耐高温性能,为高温环境下的工程应用提供了有力支持。PVD涂层技术为钟表行业带来了精美的外观和持久的保护。
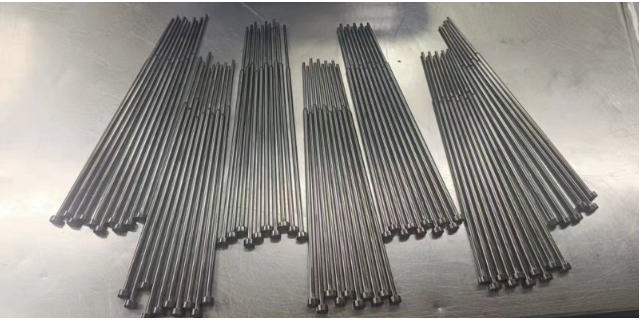
PVD涂层过程中常用的加热方式有哪些?电子束加热电子束加热是一种利用高能电子束轰击基材表面,使其迅速升温的加热方式。这种加热方式具有加热速度快、能量集中、热效率高等优点。同时,由于电子束的可控性强,可以实现对基材的局部加热,从而避免整体变形。但是,电子束加热设备复杂,成本较高,且对操作人员的技能要求相对较高。激光加热激光加热是一种利用激光束照射基材表面,使其迅速升温的加热方式。激光加热具有加热速度快、能量密度高、热影响区小等优点。与电子束加热相比,激光加热的设备成本较低,且更易于实现自动化。然而,激光加热的缺点在于其加热面积相对较小,可能需要进行多次扫描才能实现大面积加热。PVD涂层技术为汽车零部件提供了优异的抗腐蚀性能。韶关医用PVD涂层定做厂家
通过PVD涂层,可以制造出具有特殊电磁屏蔽效果的表面,保护电子设备免受电磁干扰。汕尾铝压铸PVD涂层制造商
PVD涂层提高材料硬度硬度是材料抵抗局部压力产生变形的能力。通过PVD涂层技术,可以在材料表面形成一层高硬度的涂层,如氮化钛(TiN)、碳化钛(TiC)等陶瓷涂层。这些涂层具有很高的硬度,可以明显提高基体材料的表面硬度,从而提高材料的耐磨性和抗划伤性能。增强耐磨性耐磨性是指材料在摩擦过程中抵抗磨损的能力。在许多应用场景中,如切削工具、轴承等,耐磨性是至关重要的。通过PVD涂层技术,可以在这些工具表面形成一层具有高耐磨性的涂层,减少摩擦过程中的磨损,延长工具的使用寿命。同时,PVD涂层具有良好的结合力,可以在一定程度上防止涂层脱落,进一步提高耐磨性。汕尾铝压铸PVD涂层制造商
上一篇: 深圳TIALN涂层供应商
下一篇: 佛山氮化铬涂层定制厂家