上海中高频淬火热处理加工
热处理加工在众多领域都有着而重要的应用。在汽车制造中,经过热处理的发动机零件能够承受高温高压的工作环境,提高汽车的性能和可靠性。在航空航天领域,热处理后的金属材料必须具备极高的强度和轻量化特点,以确保飞行器的安全飞行。在机械制造、建筑、电子等行业,热处理加工也为产品的质量和性能提供了有力保障。然而,热处理加工并非易事,它需要专业的技术和严格的工艺控制。温度、时间、冷却速度等参数的精细把握,直接影响着热处理的效果。只有经验丰富的技术人员和先进的设备,才能确保每一次热处理加工都能达到预期的目标。总之,热处理加工是赋予金属新生命的重要工艺。它以科学的方法和精湛的技艺,让金属在工业领域中绽放出更加耀眼的光芒。模具制造采用热处理加工,提高硬度和寿命。上海中高频淬火热处理加工
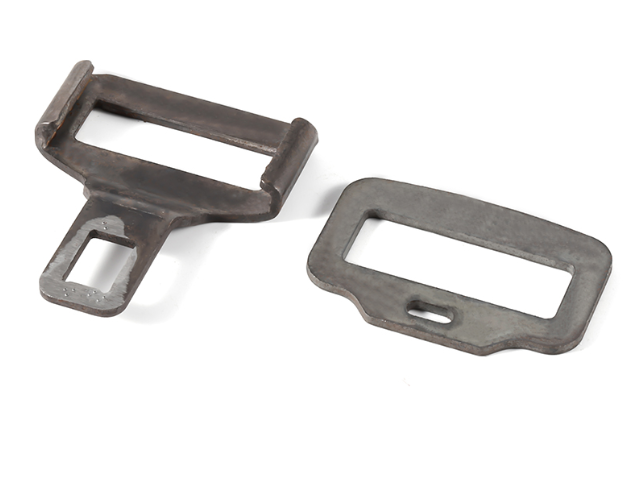
在高温的作用下,金属仿佛被注入了新的活力,为后续的变化做好准备。保温过程则如同给金属一个沉淀和调整的时间,让内部的变化更加充分和稳定。此时,金属在恒定的温度下,悄然进行着自我重塑。冷却阶段则是决定金属终性能的重要步骤。不同的冷却方式会带来截然不同的效果。快速冷却可以使金属获得更高的硬度和强度,适用于制造刀具、模具等需要高硬度的工具。而缓慢冷却则能赋予金属更好的韧性和延展性,在机械零件、结构件等领域发挥着重要作用。河南紧固件热处理加工公司热处理加工可优化金属组织结构,增强硬度、韧性及耐磨性。
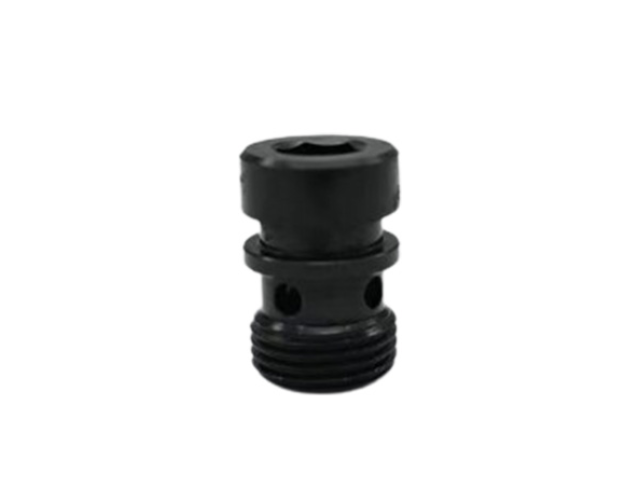
热处理加工在各个行业中都发挥着至关重要的作用。在汽车制造领域,经过热处理的发动机零件能够承受高温高压的工作环境,提高汽车的可靠性和性能。在航空航天领域,热处理后的金属材料必须具备极高的强度和轻量化特点,以确保飞行器的安全飞行。在机械制造、建筑、电子等行业,热处理加工也为产品的质量和性能提供了有力保障。然而,热处理加工并非一帆风顺,它需要严格的工艺控制和先进的设备支持。温度、时间、冷却速度等参数的微小偏差都可能影响到金属的性能。因此,热处理企业必须不断投入研发,提高技术水平,确保每一个热处理过程都能达到比较好效果。总之,热处理加工是铸就金属品质的关键工艺。它以科学的方法和精湛的技艺,为现代制造业带来了无尽的可能。
在航空航天领域,热处理后的金属材料必须具备极高的强度和轻量化特点,以确保飞行器的安全飞行。在机械制造、建筑、电子等行业,热处理加工也为产品的质量和性能提供了有力保障。然而,热处理加工并非一帆风顺,它需要严格的工艺控制和先进的设备支持。温度、时间、冷却速度等参数的微小偏差都可能影响到金属的性能。因此,热处理企业必须不断投入研发,提高技术水平,确保每一个热处理过程都能达到比较好效果。总之,热处理加工是金属的神奇锻造术。它以科学的方法和精湛的技艺,为现代工业的发展注入了强大的动力。有了热处理加工,材料性能得到有效提升。
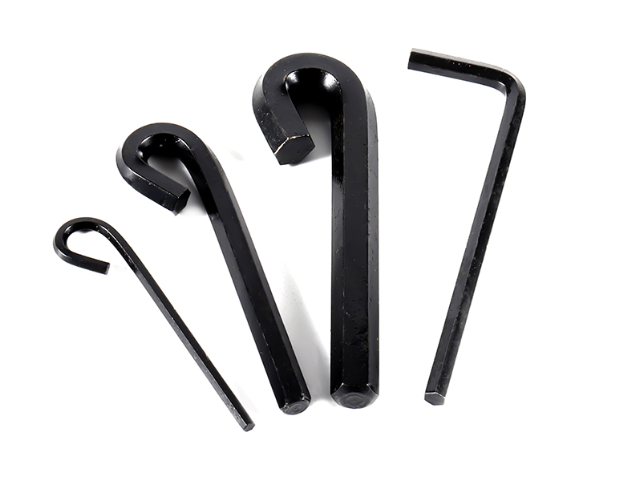
一些因素会影响回火热处理的冷却速度:一、设备条件冷却设备类型:不同的冷却设备会导致不同的冷却速度。例如,使用强制风冷设备通常比自然冷却速度快;而使用油冷或水冷设备则可以实现更快的冷却速度,但需要注意控制冷却速度以避免产生过大的热应力。设备容量和功率:设备的容量和功率大小也会影响冷却速度。较大容量和高功率的设备可能能够提供更快速的冷却,但对于小型工件可能会导致冷却过度。二、环境因素气温和湿度:周围环境的气温和湿度会影响工件的散热速度。在高温高湿的环境下,工件的冷却速度可能会变慢,因为空气的热传导能力下降。相反,在低温干燥的环境下,冷却速度可能会加快。通风情况:良好的通风条件可以促进热量的散发,从而加快冷却速度。如果在密闭空间或通风不良的环境中进行回火热处理,冷却速度可能会受到影响。三、工件的装夹方式工件之间的间距:如果工件在回火热处理时紧密排列,会影响空气的流通和热量的散发,从而降低冷却速度。适当增大工件之间的间距可以提高冷却速度。与夹具的接触面积:工件与夹具的接触面积越大,热量传导就越容易,冷却速度可能会受到影响。选择合适的夹具材料和设计,减少接触面积,可以提高冷却速度。热处理加工提升材料性能,为工业制造助力。江苏达克罗热处理加工厂
热处理加工为五金制品带来更好品质。上海中高频淬火热处理加工
在工业的宏大舞台上,紧固件宛如一颗颗关键的螺丝钉,虽看似渺小,却有着牵一发而动全身的重要性。而热处理加工,则是为这些紧固件铸就坚韧之魂的关键工艺。紧固件热处理加工是一个充满科学奥秘的过程。它起始于加热环节,根据紧固件的材质特性,如常见的中碳钢、合金钢等,将它们精细地加热到特定温度范围。这一过程如同唤醒金属内部的潜能,以中碳钢制成的螺母为例,当加热到合适温度时,其原子开始活跃,晶格结构发生变化,原本相对稳定的状态被打破,为后续的性能提升创造了条件。上海中高频淬火热处理加工
上一篇: 河南酸洗热处理加工公司
下一篇: 浙江发黑热处理加工厂家