北京物联网半导体器件加工设计
半导体器件有许多封装型式,从DIP、SOP、QFP、PGA、BGA到CSP再到SIP,技术指标一代比一代先进,这些都是前人根据当时的组装技术和市场需求而研制的。总体说来,它大概有三次重大的革新:初次是在上世纪80年代从引脚插入式封装到表面贴片封装,极大地提高了印刷电路板上的组装密度;第二次是在上世纪90年代球型矩正封装的出现,它不但满足了市场高引脚的需求,而且极大地改善了半导体器件的性能;晶片级封装、系统封装、芯片级封装是第三次革新的产物,其目的就是将封装减到很小。每一种封装都有其独特的地方,即其优点和不足之处,而所用的封装材料,封装设备,封装技术根据其需要而有所不同。驱动半导体封装形式不断发展的动力是其价格和性能。高纯度的多晶硅溶解后掺入硅晶体晶种,然后慢慢拉出,形成圆柱形的单晶硅。北京物联网半导体器件加工设计
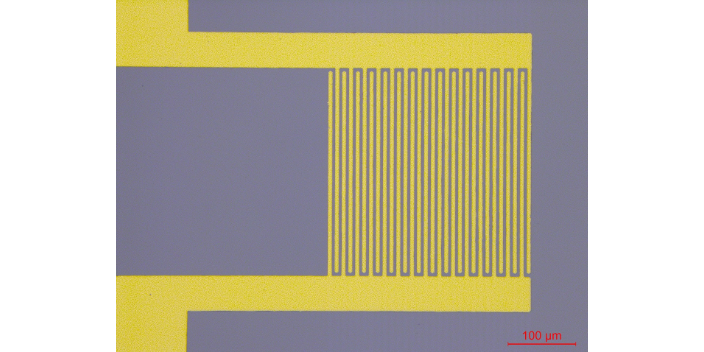
纳米技术有很多种,基本上可以分成两类,一类是由下而上的方式或称为自组装的方式,另一类是由上而下所谓的微缩方式。前者以各种材料、化工等技术为主,后者则以半导体技术为主。以前我们都称 IC 技术是「微电子」技术,那是因为晶体管的大小是在微米(10-6米)等级。但是半导体技术发展得非常快,每隔两年就会进步一个世代,尺寸会缩小成原来的一半,这就是有名的摩尔定律(Moore’s Law)。到了 2001 年,晶体管尺寸甚至已经小于 0.1 微米,也就是小于 100 纳米。因此是纳米电子时代,未来的 IC 大部分会由纳米技术做成。但是为了达到纳米的要求,半导体制程的改变须从基本步骤做起。每进步一个世代,制程步骤的要求都会变得更严格、更复杂。广州半导体器件加工流程芯片封装后测试则是对封装好的芯片进行性能测试,以保证器件封装后的质量和性能。
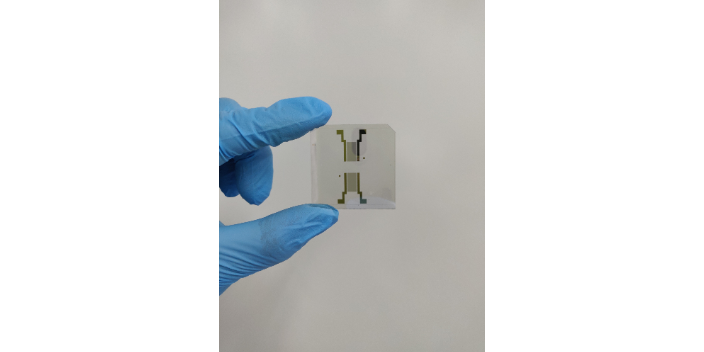
半导体器件加工是指将半导体材料加工成具有特定功能的器件的过程。它是半导体工业中非常重要的一环,涉及到多个步骤和工艺。下面将详细介绍半导体器件加工的步骤。1. 半导体材料准备:半导体器件加工的第一步是准备半导体材料。常用的半导体材料有硅(Si)、砷化镓(GaAs)、磷化镓(GaP)等。这些材料需要经过精细的制备过程,包括材料的提纯、晶体生长、切割和抛光等。2. 清洗和去除表面杂质:在半导体器件加工过程中,杂质会对器件的性能产生负面影响。因此,在加工之前需要对半导体材料进行清洗和去除表面杂质的处理。常用的清洗方法包括化学清洗和物理清洗。
半导体器件加工是指将半导体材料加工成具有特定功能的器件的过程。它是半导体工业中非常重要的一环,涉及到多个步骤和工艺。下面将详细介绍半导体器件加工的步骤。蚀刻:蚀刻是将光刻图案转移到晶圆上的关键步骤。蚀刻是利用化学反应将不需要的材料从晶圆表面去除的过程。常用的蚀刻方法包括湿蚀刻和干蚀刻。沉积:沉积是在晶圆表面上形成薄膜的过程。沉积可以通过物理的气相沉积(PVD)、化学气相沉积(CVD)、溅射沉积等方法实现。沉积的薄膜可以用于形成导电层、绝缘层或金属层等。MEMS器件以硅为主要材料。
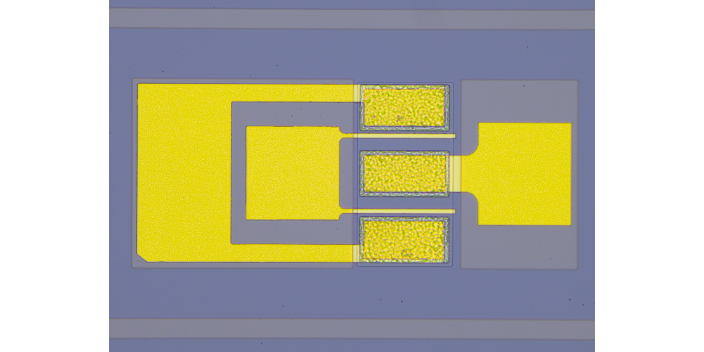
半导体技术进入纳米时代后,除了水平方向尺寸的微缩造成对微影技术的严苛要求外,在垂直方向的要求也同样地严格。一些薄膜的厚度都是1~2纳米,而且在整片上的误差小于5%。这相当于在100个足球场的面积上要很均匀地铺上一层约1公分厚的泥土,而且误差要控制在0.05公分的范围内。蚀刻:另外一项重要的单元制程是蚀刻,这有点像是柏油路面的刨土机或钻孔机,把不要的薄层部分去除或挖一个深洞。只是在半导体制程中,通常是用化学反应加上高能的电浆,而不是用机械的方式。在未来的纳米蚀刻技术中,有一项深度对宽度的比值需求是相当于要挖一口100公尺的深井,挖完之后再用三种不同的材料填满深井,可是每一层材料的厚度只有10层原子或分子左右。这也是技术上的一大挑战。半导体硅片制造包括硅单晶生长、切割、研磨、抛光、研磨、清洗、热处理、外延、硅片分析等多个环节。北京新材料半导体器件加工好处
半导体芯片封装完成后进行成品测试,通常经过入检、测试和包装等工序,较后入库出货。北京物联网半导体器件加工设计
半导体技术的演进,除了改善性能如速度、能量的消耗与可靠性外,另一重点就是降低其制作成本。降低成本的方式,除了改良制作方法,包括制作流程与采用的设备外,如果能在硅芯片的单位面积内产出更多的 IC,成本也会下降。所以半导体技术的一个非常重要的发展趋势,就是把晶体管微小化。当然组件的微小化会伴随着性能的改变,但很幸运的,这种演进会使 IC 大部分的特性变好,只有少数变差,而这些就需要利用其它技术来弥补了。半导体制程有点像是盖房子,分成很多层,由下而上逐层依蓝图布局迭积而成,每一层各有不同的材料与功能。北京物联网半导体器件加工设计
上一篇: 湖南新型半导体器件加工工厂
下一篇: 河北半导体器件加工哪家有