河南汽车压铸模具生产厂家
使用与维护正确的使用和维护是提高压铸模具使用寿命的关键。在使用过程中,应遵循以下原则:规范操作:操作人员应熟悉模具的使用方法和注意事项,遵循操作规程,避免因操作不当导致模具损坏。合理选择润滑剂和脱模剂:润滑剂和脱模剂的选择对模具的使用寿命具有重要影响。应根据模具的材料、工作环境和使用要求等因素,合理选择润滑剂和脱模剂。定期清洁与保养:定期对模具进行清洁和保养,去除表面的污垢和金属残渣,保持模具的清洁和光滑。同时,对模具的关键部位进行定期检查和维护,及时发现并解决潜在问题。适时更换易损件:模具在使用过程中,部分易损件如导柱、导套等会出现磨损或变形。应及时更换这些易损件,避免对整个模具造成更大的损害。压铸模具的使用寿命可以通过热处理和表面涂层技术来延长。河南汽车压铸模具生产厂家
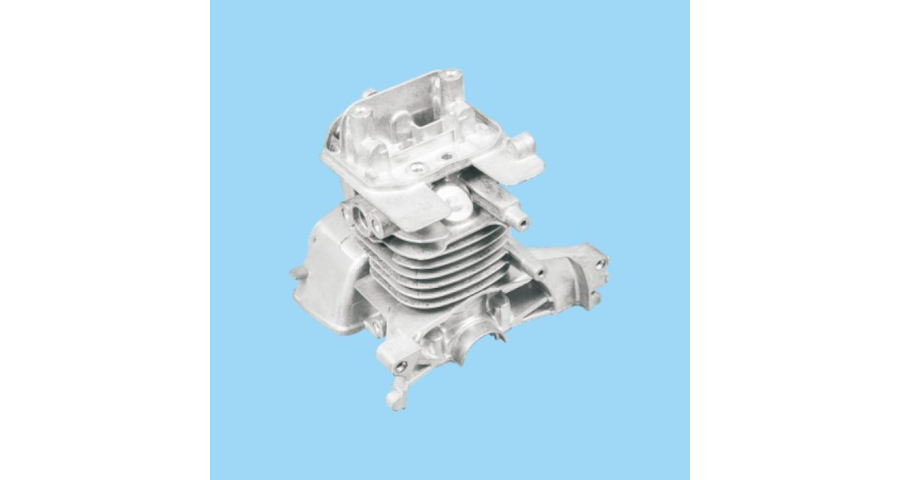
通过采用先进的加工技术,如精密铸造、热处理、表面处理等,可以改善材料的性能,提高模具的精度和耐用性。例如,热处理可以改变材料的金相结构,提强高度和硬度;表面处理可以增强模具的耐磨性和耐腐蚀性。此外,加强模具的维护和保养也是解决材料问题的重要措施。定期对模具进行检查和维修,及时发现并处理潜在问题,可以延长模具的使用寿命。同时,对于磨损严重的模具部件,应及时进行更换或修复,避免影响整个模具的性能。引入新材料和新技术也是解决材料问题的有效途径。随着科技的不断发展,新型模具材料和加工技术不断涌现。通过引进这些新材料和新技术,可以进一步提高模具的质量和性能,满足不断变化的市场需求。综上所述,解决压铸模具制造过程中的材料问题需要从多个方面入手,包括选择合适的材料、控制材料质量、优化加工工艺、加强维护和保养以及引入新材料和新技术等。通过这些措施的实施,可以确保模具的质量、性能和寿命达到比较好状态。北京加工压铸模具结构压铸模具的高效散热设计有助于缩短生产周期和提高铸件的机械性能。
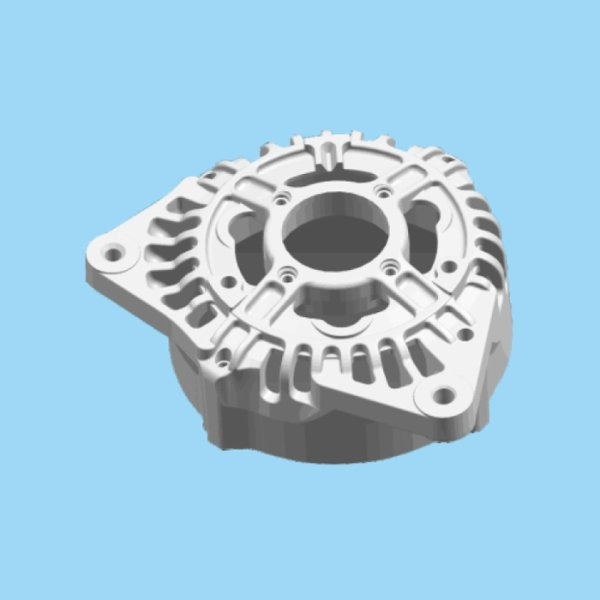
导向与定位机构:确保定模和动模在合模过程中的精确对位,防止错位和飞边。顶出机构:用于将凝固后的零件从模具中顶出,便于取件。压铸模具的设计要点在设计压铸模具时,需要考虑以下要点:模具材料的选择:应根据零件的材料、生产批量和模具寿命等因素,选择合适的模具材料。分型面的确定:分型面的选择直接影响到模具的结构和零件的脱模。浇道和排气系统的设计:合理的浇道设计可以确保金属流动顺畅,排气系统则有助于排除型腔内的气体,防止气泡产生。
修复方法可以根据具体情况选择,如磨损部分可以进行打磨或补焊,裂纹部分可以进行焊接或加固。修复过程中应注意技术要求,确保修复后的模具能够满足使用要求。防止模具生锈:模具在存放或暂时停用期间,容易受到潮湿环境的影响而生锈。生锈不仅影响模具的外观,还会降低模具的使用寿命。为了防止模具生锈,可以在模具表面涂抹一层防锈剂,并将其放置在干燥通风的地方,避免受潮。此外,定期检查模具的存放环境,确保其处于良好的状态,也是防止模具生锈的有效措施。保持模具润滑:模具的零部件在工作时需要润滑以减少摩擦和磨损。因此,定期给模具进行润滑维护是非常重要的。宁波双耀机械有限公司致力于提供 压铸模具,欢迎您的来电哦!
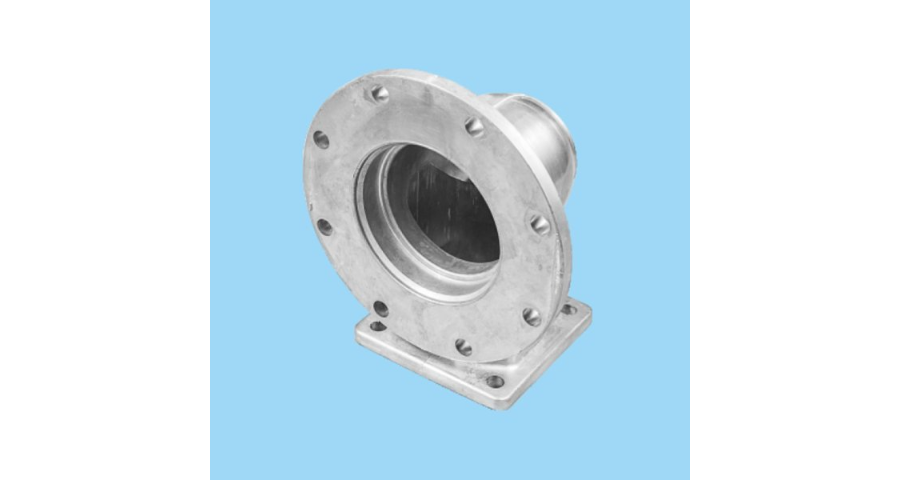
结构设计合理的结构设计是提高压铸模具使用寿命的重要保障。在结构设计时,应遵循以下原则:简化结构:在满足使用要求的前提下,应尽量简化模具结构,减少不必要的加工和装配环节,降低模具的制造成本和使用难度。合理分布应力:通过合理的结构设计,使模具在使用过程中应力分布均匀,避免局部应力过大导致模具损坏。优化分型面设计:分型面是模具设计中的关键部位,其设计合理与否直接影响到铸件的脱模和模具的使用寿命。因此,应充分考虑铸件的形状、尺寸和脱模方式等因素,设计出合理的分型面。预留足够的强度和刚度:在设计过程中,应预留足够的强度和刚度,以应对模具在使用过程中可能出现的各种应力。压铸模具是压铸工艺中的重要组成部分,是实现压铸成型的关键工具。福建整套压铸模具价格
在模具设计中,考虑金属收缩率是确保铸件尺寸准确的关键因素。河南汽车压铸模具生产厂家
技术创新与升级随着科技的不断发展,新的技术和工艺不断涌现,为提高压铸模具的使用寿命提供了更多的可能性。企业应关注新技术和新工艺的发展趋势,积极引进和应用先进技术,推动压铸模具的技术创新和升级。例如,采用先进的数值模拟技术对模具设计进行优化,采用3D打印技术制造复杂结构的模具,采用表面处理技术提高模具的耐磨性和耐腐蚀性等。培训与人员管理提高压铸模具使用寿命,除了上述的物质和技术层面的措施外,人员的管理和培训也是不可忽视的一环。加强操作人员培训:定期对操作人员进行模具使用、维护和保养方面的培训,使其了解模具的结构、性能和使用方法,提高操作技能和责任意识。河南汽车压铸模具生产厂家
上一篇: 广东压铸模具结构
下一篇: 宁波机械压铸模具价格