环氧基偶联剂成分情况
偶联剂可以通过改善塑料的表面能来提高其导电性能。在塑料加工过程中,熔体与模具、设备等接触表面会产生摩擦热,导致熔体温度升高。而较高的熔体温度会导致塑料分子链的热运动加剧,使熔体的电阻率增加。为了解决这个问题,可以在塑料中添加适量的偶联剂。偶联剂可以作为分散剂,将熔体中的颗粒分散均匀,减小熔体的表面积,从而降低熔体的温度。同时,偶联剂还可以在熔体表面形成一层润滑膜,减少熔体与模具、设备等接触表面的摩擦系数,进一步降低熔体的温度和电阻率。偶联剂可以改善塑料的可加工性,使其更容易进行模塑、吹塑等加工工艺。环氧基偶联剂成分情况
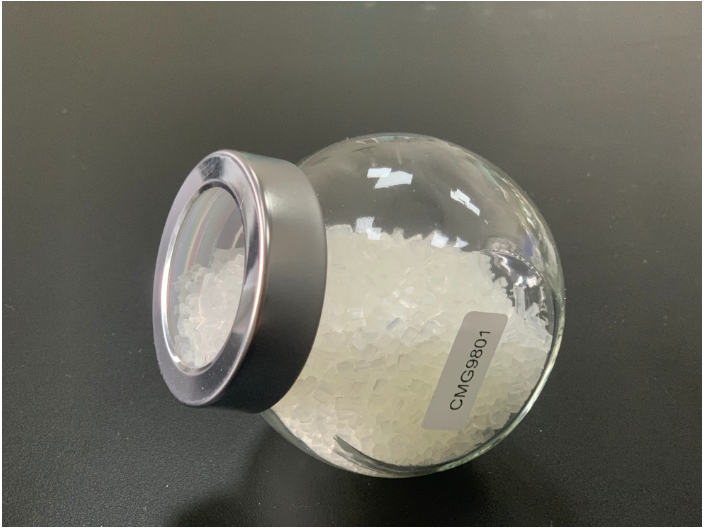
偶联剂可以提高塑料制品的表面性能。在塑料制品的回收过程中,表面性能是一个关键因素,直接影响到塑料制品的回收效果。传统的塑料制品表面光滑度较低,容易粘连在一起,导致回收过程中的杂质去除困难。而偶联剂可以通过与塑料制品中的添加剂或填料发生化学反应,形成化学键或物理吸附作用,从而提高塑料制品的表面性能。这样,塑料制品在回收过程中就更容易与其他废料分离,提高回收效率。偶联剂可以降低塑料制品的相容性。在塑料制品的回收过程中,不同种类的塑料往往难以混合在一起,导致回收效率降低。而偶联剂可以通过与塑料中的添加剂或填料发生化学反应,形成稳定的化合物,从而降低塑料之间的相容性。这样,不同类型的塑料制品就可以更容易地分离和回收,提高整体回收效率。环氧基偶联剂成分情况在塑料加工中使用偶联剂可以减少气泡的产生,提高产品的表面平整度。

偶联剂可以提高塑料的阻燃性能。在塑料制品的生产过程中,通常需要添加一定量的阻燃剂来提高塑料的阻燃性能。然而,由于阻燃剂与塑料之间的相容性较差,导致阻燃效果不理想。而偶联剂可以通过改善塑料与其他材料的界面性能,使阻燃剂与塑料之间的相容性得到显著提高,从而提高阻燃剂在塑料中的分散性和稳定性,进一步提高塑料的阻燃性能。偶联剂可以提高塑料的热稳定性。在塑料制品的使用过程中,高温是导致其燃烧的主要原因之一。而偶联剂可以有效地降低塑料的熔融温度和热分解温度,减小塑料在高温下的热变形和降解程度,从而提高塑料的热稳定性,使其在高温环境下更不容易燃烧。
偶联剂可以改善填充剂与合成树脂之间的界面相容性。填充剂与合成树脂之间的界面相容性对于填充剂的分散度和塑料制品的性能具有重要影响。如果填充剂与合成树脂之间的界面相容性差,会导致填充剂的分散度降低,从而影响塑料制品的性能。而偶联剂可以通过与填充剂表面的活性基团发生化学反应或物理吸附作用,形成一种稳定的化学键合,从而改善填充剂与合成树脂之间的界面相容性。除了降低合成树脂熔体的粘度和改善填充剂的分散度外,偶联剂还可以提高塑料制品的硬度、耐磨性、抗静电性等性能。这是因为偶联剂可以在填充剂和合成树脂之间形成一层致密的化学键合层,这层化学键合层可以提高填充剂的稳定性和耐久性,从而提高塑料制品的性能。使用偶联剂可以改善塑料的抗紫外线性能,延缓产品老化速度。
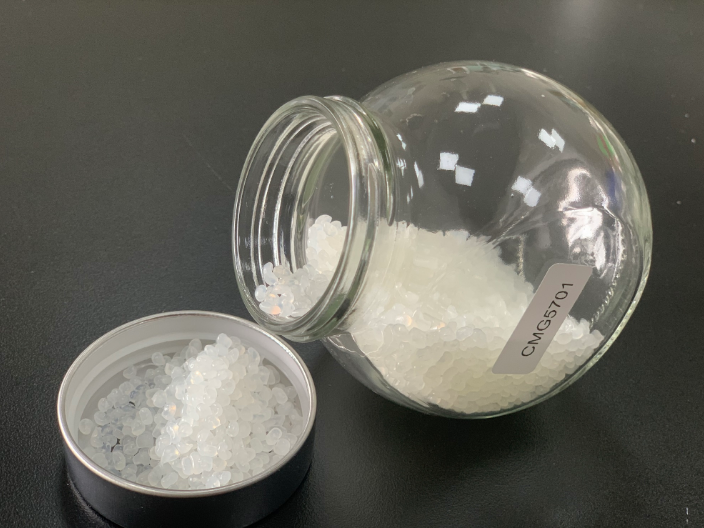
使用偶联剂可以有效降低塑料的吸水率,提高其尺寸稳定性。塑料在长期使用过程中,容易受到环境湿度的影响而吸水,导致尺寸变化、变形甚至破裂。而偶联剂的添加可以改善塑料的吸水性能,提高其尺寸稳定性,从而延长塑料制品的使用寿命。偶联剂是一种能够在有机物和无机物之间建立化学键的物质。在塑料制品中,偶联剂可以与塑料分子以及填充物之间形成化学键,从而增强塑料的结构稳定性。偶联剂的添加可以改变塑料的表面性质,减少塑料与水分子之间的相互作用,降低塑料的吸水率。偶联剂能够提高塑料的耐化学品性能,延长使用寿命。环氧基偶联剂成分情况
偶联剂能够提高塑料的抗拉强度和抗压强度。环氧基偶联剂成分情况
偶联剂在塑料中的应用有哪些?1.增强塑料的力学性能:偶联剂在塑料中的主要作用之一是增强塑料的力学性能。通过与塑料分子链的交联作用,偶联剂能够提高塑料的强度、硬度和耐磨性。例如,在聚乙烯中添加偶联剂可以显著提高其拉伸强度和冲击强度,使其更适用于强度高要求的应用领域。2.改善热稳定性:塑料在高温环境下容易发生热分解,导致性能下降甚至失效。偶联剂可以通过与塑料分子链的交联作用,提高塑料的热稳定性。例如,聚丙烯中添加偶联剂可以有效抑制其在高温下的热分解,延长塑料的使用寿命。3.提高耐候性:塑料在户外环境中容易受到紫外线、氧气和湿气等因素的影响,导致颜色变化、表面龟裂等问题。偶联剂可以与塑料分子链形成稳定的化学键,提高塑料的耐候性。例如,聚氯乙烯中添加偶联剂可以有效抵抗紫外线的侵蚀,延长塑料的使用寿命。4.促进填充剂的分散:在塑料中添加填充剂可以降低成本、改善力学性能和改变塑料的特性。然而,填充剂的分散性对塑料的性能影响很大。偶联剂可以作为填充剂与塑料分子链之间的桥梁,促进填充剂的分散,提高塑料的综合性能。环氧基偶联剂成分情况
上一篇: 浙江环氧增韧剂
下一篇: 长沙改性pp增韧剂价格多少