资阳汽车覆盖件冲压模修模
数控车削加工中的切削用量包括背吃刀量ap、主轴转速S(或切削速度υ)及进给速度F(或进给量f)。切削用量的选择原则,合理选用切削用量对提高数控车床的加工质量至关重要。确定数控车床的切削用量时一定要根据机床说明书中规定的要求,以及刀具的耐用度去选择,也可结合实际经验采用类比法来确定。一般的选择原则是:粗车时,首先考虑在机床刚度允许的情况下选择尽可能大的背吃刀量ap;其次选择较大的进给量f;然后再根据刀具允许的寿命确定一个合适的切削速度υ。增大背吃刀量可减少走刀次数,提高加工效率,增大进给量有利于断屑。精车时,应着重考虑如何保证加工质量,并在此基础上尽量提高加工效率,因此宜选用较小的背吃刀量和进给量,尽可能地提高加工速度。主轴转速S(r/min)可根据切削速度υ(mm/min)由公式S=υ1000/πD(D为工件或刀/具直径mm)计算得出,也可以查表或根据实践经验确定。五金精密件加工研发-上海琨盛精密机械有限公司。资阳汽车覆盖件冲压模修模
模具
慢走丝加工面修不光:1.相对偏移量过小。——适当增加相对偏移量。2.工件材料变形导致修切时切割速度不均匀。——合理安排工艺,减小材料变形。3.电极丝的质量差。建议使用原装耗材。4.导丝部太脏。——对导丝部进行维护保养。5.导电块磨损严重。将导电块旋转或更换。6.工艺参数选择错误。——正确输入相关的加工要求,生成合理的工艺文件。7.冲液状态不好,达不到标准冲液压力及喷流形状。——检查上、下喷嘴是否损坏,如果有损坏,应及时更换。丽水多工位模具安装螺杆螺套研发定制-上海琨盛精密。
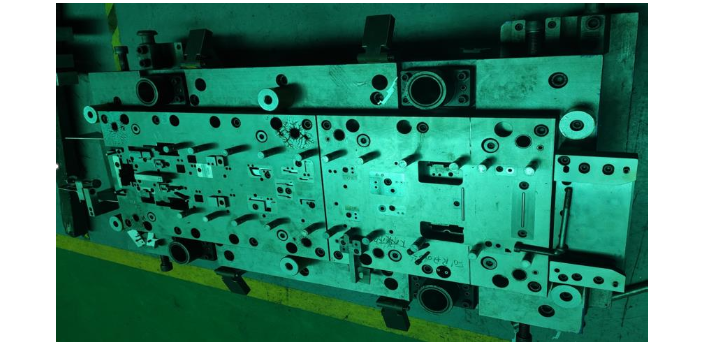
工序划分的原则:在数控车床上加工零件,常用的工序的划分原则有两种。(1)保持精度原则。工序一般要求尽可能地集中,粗、精加工通常会在一次装夹中全部完成。为减少热变形和切削力变形对工件的形状、位置精度、尺寸精度和表面粗糙度的影响,则应将粗、精加工分开进行。(2)提高生产效率原则。为减少换刀次数,节省换刀时间,提高生产效率,应将需要用同一把刀加工的加工部位都完成后,再换另一把刀来加工其他部位,同时应尽量减少空行程。
磨床砂轮:粒度每个砂轮都有一个表示该特性的数字,粒度则是指砂轮中单个磨粒的大小。该数字对应一英吋平方大小的筛网中,所含有的目数。换句话说,数字大表示磨料通过的筛孔较小(磨料较细)。较小的数字(例如10、16或24)表示砂轮使用的磨料较粗。颗粒越粗,能去除的工件碎屑就越大。较粗的磨料可用于快速去除工件体积,但加工表面粗糙度较差。较大的数字(例如70、100和180),则表示砂轮使用的磨料较细。细砂轮适用于要求精细的表面粗度、接触面小或坚硬、易碎的材料加工上。无论是金属、塑料,还是陶瓷或玻璃,都可以通过模具进行加工和成型。
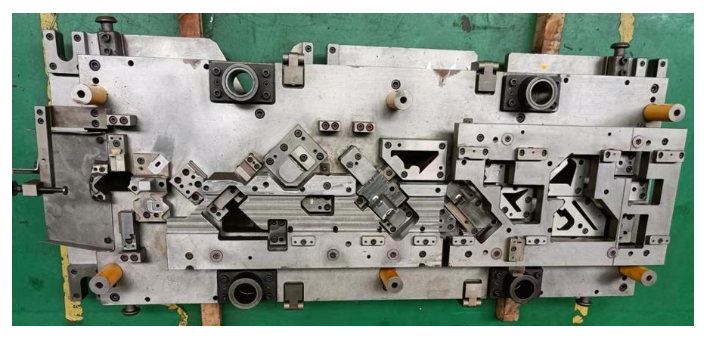
刀具的使用寿命除与刀具材料相关外,还与刀具的直径有很大的关系。刀具直径越大,能承受的切削用量也越大。所以在零件形状允许的情况下,采用尽可能大的刀具直径是延长刀具寿命,提高生产率的有效措施。数控车削常用的刀具一般分为3类。即尖形车刀、圆弧形车刀和成型车刀。(1)尖形车刀。以直线形切削刃为特征的车刀一般称为尖形车刀。其刀尖由直线性的主、副切削刃构成,如外圆偏刀、端面车刀等。这类车刀加工零件时,零件的轮廓形状主要由一个单独的刀尖或一条直线形主切削刃位移后得到。(2)圆弧形车刀。除可车削内外圆表面外,特别适宜于车削各种光滑连接的成型面。其特征为:构成主切削刃的刀刃形状为一圆度误差或线轮廓误差很小的圆弧,该圆弧刃的每一点都是圆弧形车刀的刀尖,因此刀位点不在圆弧上,而在该圆弧的圆心上。(3)成型车刀。即所加工零件的轮廓形状完全由车刀刀刃的形状和尺寸决定。数控车削加工中,常用的成型车刀有小半径圆弧车刀、车槽刀和螺纹车刀等。为了减少换刀时间和方便对刀,便于实现机械加工的标准化。数控车削加工中,应尽量采用机夹可转位式车刀。非标研发定制-上海琨盛精密机械有限公司。连云港高速冲压模具加工厂
汽车精密配件加工厂-上海琨盛精密。资阳汽车覆盖件冲压模修模
检具的定义1、检具是一种用来测量和评价零件尺寸、形状、位置特性质量的特用检验设备。2、检具的作用①通过检具实现对零件的在线检测;通过目测,或测量表,或卡尺对零件型面,周边进行检查,借助检验销或目测对零件上不同性质的孔及零件与零件之间的联接位置进行目检,从而保证在试生产及起步生产时实现零件质量状态的快速判断。②对于零件上的某些极其重要的功能性尺寸,还能利用检具进行数值检测。通常不能借助检具直接获得零件基于车身坐标系统精确的坐标值,而是将零件置于检具上通过三坐标测量机测量方才获得。现代检具的结构在设计时同时考虑其可以作为测量支架使用。钣金零件检具对零件的质量控制起着决定性的作用。资阳汽车覆盖件冲压模修模
上一篇: 苏州汽车覆盖件冲压模修模
下一篇: 金华单工模具开发