多功能脱模剂材料
脱模剂的外观可以反映出其质量。高质量的脱模剂通常具有较好的均匀性和透明度。如果脱模剂呈现出浑浊、稠密或不均匀的状态,那么其质量可能较差。此外,脱模剂的颜色也可以帮助判断其质量。一般来说,透明或半透明的脱模剂质量较好,而颜色深或不透明的脱模剂可能存在质量问题。脱模剂的挥发性是指在一定温度下,脱模剂从液体变为气体的过程。挥发性好的脱模剂可以更快地渗透到模具表面,从而提高生产效率。一般来说,挥发性越好的脱模剂质量越好。可以通过观察脱模剂的表面是否有油状物残留来判断其挥发性。如果表面有油状物残留,说明脱模剂挥发性较差,质量可能较差。树脂砂脱模剂具有比较好的热稳定性和化学稳定性,能够在高温和高压下保持良好的脱模性能。多功能脱模剂材料
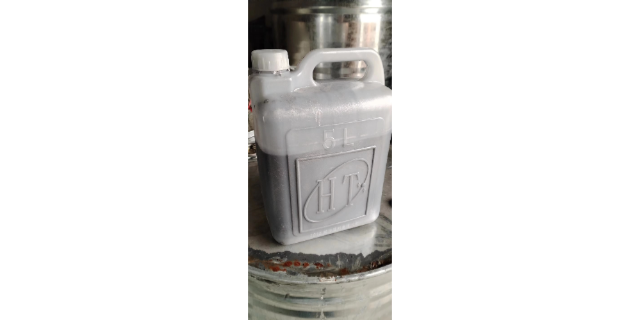
脱模剂的使用方法因材料和成型条件而异。以下是一些常见的使用方法——喷涂法:将脱模剂均匀地喷洒在模具表面,然后进行成型操作。这种方法适用于大型模具和复杂形状的成型件。喷涂法可以使脱模剂更均匀地分布在模具表面,从而提高润滑效果。刷涂法:将脱模剂涂抹在模具表面,然后用刷子或其他工具将其均匀涂抹开。这种方法适用于小型模具和较简单的成型件。刷涂法可以使脱模剂更深入地渗透到模具表面,从而提高润滑效果。浸泡法:将成型材料浸入脱模剂中,使其充分吸收脱模剂。这种方法适用于成型材料容易与模具粘附的情况。浸泡法可以使脱模剂更充分地分布在成型材料中,从而提高润滑效果。多功能脱模剂材料脱模剂的主要目的是防止橡胶、塑料等材料在模具中固化或与模具表面产生粘连。
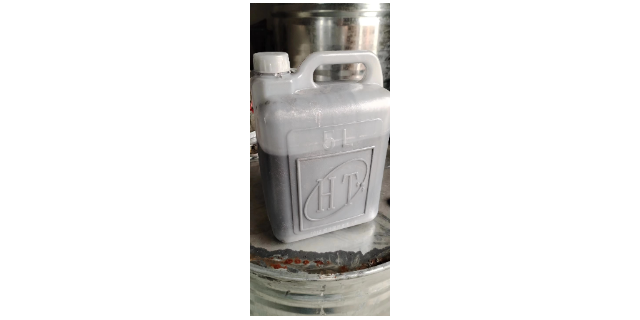
随着工业化的快速发展,脱模剂已成为各种制造过程中不可或缺的一部分。然而,传统的脱模剂往往含有有害化学物质,对环境造成了严重影响。因此,环保脱模剂的研发和应用越来越受到重视。脱模剂的主要作用是在模具表面形成一层薄膜,防止熔融金属或塑料与模具直接接触,从而避免损坏模具或产生瑕疵。在许多制造过程中,如塑料、橡胶、金属铸造等,脱模剂都起着至关重要的作用。然而,传统的脱模剂通常含有有毒化学物质,如氯氟烃(CFCs)、硅油和其他挥发性有机化合物(VOCs)。这些物质在使用过程中会释放到空气中,对环境和人体健康造成潜在威胁。此外,这些有害物质还会在生产过程中积累,导致环境污染和资源浪费。
定期更换脱模剂——观察脱模剂的状态:定期检查脱模剂的状态,如颜色、粘度、气味等,发现异常应及时更换。评估脱模剂的效果:通过对比新旧脱模剂的脱模效果,评估脱模剂的使用寿命,发现使用寿命过长的应提前更换。记录脱模剂的使用情况:记录每次更换脱模剂的时间、原因以及更换后的效果,为下一次更换提供参考依据。脱模剂使用的注意事项——储存条件:脱模剂应储存在阴凉、干燥的地方,避免阳光直射和高温环境,以免影响脱模剂的性能。安全操作:使用脱模剂时要注意安全防护,避免皮肤接触和吸入,如有意外情况发生,应立即用大量水冲洗。环保要求:选择环保型的脱模剂,减少对环境的污染。为了保持脱模剂的品质稳定,建议将其垂直放置。
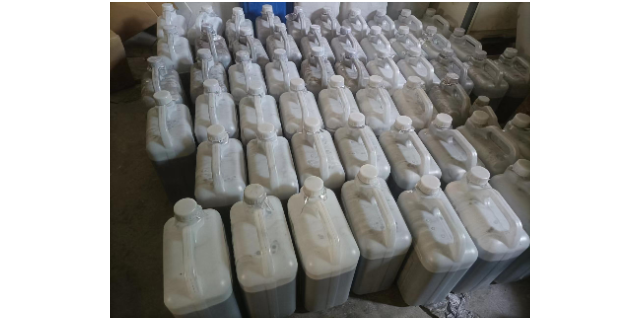
耐高温脱模剂的基本原理是在模具表面形成一层薄膜,该薄膜具有抗粘性和润滑性,可以有效地提高模具的脱模效果。耐高温脱模剂通常由多种组分构成,包括成膜剂、抗氧剂、润滑剂等。其中,成膜剂是形成脱模剂薄膜的主要成分,它需要在高温下保持稳定,不易分解或挥发。抗氧剂的作用是预防脱模剂在高温下氧化,从而提高其稳定性。润滑剂则可以降低模具表面能,减小脱模阻力,使产品更容易脱离模具。生产工艺上,耐高温脱模剂一般采用乳化、混合、喷雾干燥等技术进行制备。这些技术可以确保脱模剂的组分在高温下保持稳定,并具有较长的使用寿命。此外,为了满足不同行业的需求,耐高温脱模剂往往需要具有一定的耐腐蚀性、绝缘性等特点,从而能够适应各种复杂环境。树脂砂脱模剂适用于各种类型的树脂砂、水玻璃砂等铸造工艺,应用范围广。多功能脱模剂材料
脱模剂的性能直接影响到产品的质量和生产效率。多功能脱模剂材料
喷涂脱模剂:将稀释后的脱模剂装入喷雾器中,均匀喷在模具表面。喷涂时要注意喷枪与模具的距离,保持适当的距离,以便脱模剂能充分覆盖模具表面。喷涂厚度一般为2-3mm,具体厚度可根据模具结构和成型条件进行调整。刷涂脱模剂:对于复杂结构的模具,可以采用刷涂的方式涂抹脱模剂。刷涂时要确保刷子与模具表面接触均匀,避免出现漏刷或刷过多的情况。刷涂厚度同样可以根据模具结构和成型条件进行调整。预热模具:在成型前,需要对模具进行预热,以提高模具温度,有利于脱模剂充分发挥作用。预热温度根据模具材料和成型条件进行调整,通常在60-120℃之间。成型:将预先准备好的原料加入模具中,进行成型。成型过程中要控制好压力、速度、温度等参数,以保证成型质量和成品率。后处理:成型完成后,对成品进行切割、打磨、清洗等后处理工序。在这个过程中要避免使用硬物刮擦模具表面,以免损伤模具。多功能脱模剂材料
上一篇: 山东快速封箱胶
下一篇: 天津高密封性封箱泥条