车间5S/6S
5S/6S精细化管理是一种用于改善工作环境和提高工作效率的管理方法。它通过整理、整顿、清扫、清洁和素养的五个步骤,以及安全的第六个步骤,来建立和维护一个有序、整洁、高效和安全的工作环境。将5S/6S精细化管理与企业的整体战略和目标相结合,可以带来以下好处:1.提高生产效率:通过整理和整顿工作区域,减少浪费和不必要的移动,提高工作效率和生产能力。2.优化质量控制:通过清洁和清扫工作区域,减少污染和杂乱,提高产品质量和一致性。3.提升员工参与度:通过培养员工的素养和安全意识,增强员工的责任感和参与度,促进团队合作和员工满意度。4.降低事故风险:通过安全管理措施,减少工作场所的事故风险,保护员工的安全和健康。为了将5S/6S精细化管理与企业的整体战略和目标相结合,以下几点是值得注意的:1.将5S/6S精细化管理纳入企业的战略规划和目标设定中,确保其与其他管理方法和流程相互配合和协调。2.培训和教育员工,使其了解5S/6S精细化管理的重要性和价值,并激发他们的参与和支持。3.设立明确的指标和目标,用于评估和监控5S/6S精细化管理的实施效果,并与企业的绩效评估和奖励体系相结合。通过5S/6S管理,工厂可以改善生产线的布局和流程,减少物料和信息的传递时间。车间5S/6S
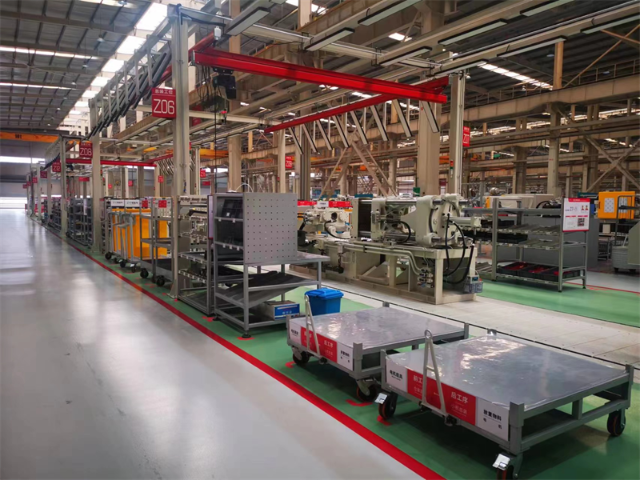
要在工厂中推行标准化的5S/6S作业流程,可以按照以下步骤进行:1.培训和意识提高:首先,对所有员工进行5S/6S的培训,让他们了解5S/6S的概念、原则和目标。提高员工对标准化作业流程的重要性和好处的认识。2.制定5S/6S策略:制定一个明确的5S/6S策略,包括目标、时间表和责任分工。确保每个员工都知道自己在5S/6S实施中的角色和职责。3.分类和整理:开始时,对工作区域进行分类和整理。清理不必要的物品,将工作区域划分为不同的区域,并为每个区域指定一个负责人。4.整顿和清洁:确保工作区域的整顿和清洁。为每个工作区域制定清洁标准,并制定清洁计划。培养员工保持工作区域整洁和清洁的习惯。5.标准化:制定标准化工作程序和操作规范。确保每个员工都按照相同的标准进行工作,减少差异性和错误。6.维护和改进:建立一个维护和改进机制,定期检查和评估5S/6S的实施情况。收集员工的反馈和建议,并根据需要进行改进。7.持续改进:将5S/6S作为一个持续改进的过程来看待。鼓励员工提出改进意见,并及时采纳和实施。杭州工厂精益5S/6S管理培训机构通过5S/6S管理,工厂可以提高生产线的可追溯性和质量控制能力,降低产品质量问题的发生率。
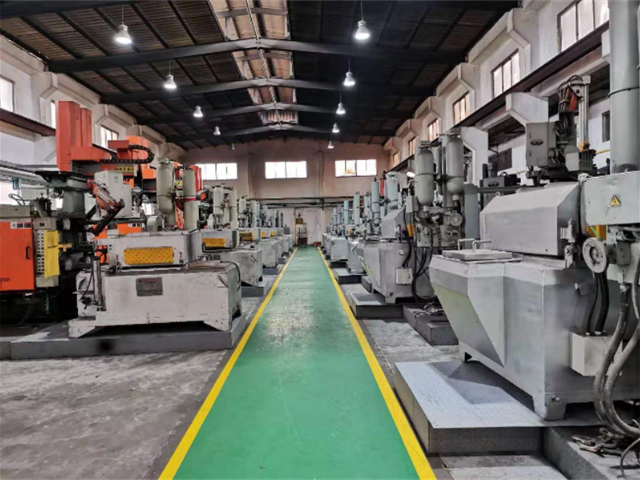
将5S/6S与员工的日常工作和生产活动相结合是非常重要的,这样可以确保5S/6S的实施不会干扰正常的工作流程。以下是一些方法可以帮助实现这一目标:1.培训和意识提高:提供5S/6S的培训,确保员工了解其目的和好处。解释如何将5S/6S原则应用于他们的日常工作中,并鼓励他们参与其中。2.制定明确的标准和责任:确保每个员工都知道他们在5S/6S实施中的角色和责任。制定明确的标准和指导方针,以便员工可以根据这些标准进行操作。3.集体参与:鼓励员工参与5S/6S活动,例如定期的清理和整理工作区域。可以设立奖励机制,以激励员工积极参与。4.整合到日常工作流程中:将5S/6S原则纳入到日常工作流程中,例如在每个工作日开始和结束时进行短暂的整理和清理。确保员工将5S/6S作为日常工作的一部分,而不是额外的负担。5.持续改进:鼓励员工提出改进意见,并将其纳入到5S/6S实施中。定期评估和审查5S/6S的效果,并根据反馈进行调整和改进。
工厂5S/6S管理培训的主要内容和方法如下:主要内容:1.5S/6S概述:介绍5S/6S管理的背景、目的和重要性。2.5S/6S原则:详细解释5S/6S的五个原则,即整理、整顿、清扫、清洁和素养。3.5S/6S步骤:介绍每个步骤的具体操作和实施方法,包括整理工作区、标识物品、设立标准、清洁工作区和保持纪律。4.5S/6S工具和技术:介绍一些常用的工具和技术,如5S/6S检查表、5S/6S标识、5S/6S培训材料等。5.5S/6S维护和持续改进:讲解如何持续维护和改进5S/6S管理,包括定期检查、培训和奖励机制等。主要方法:1.理论讲解:通过讲解5S/6S的原理、步骤和工具,使学员了解其基本概念和操作方法。2.实地演示:带领学员到实际工作现场,展示如何进行5S/6S管理,并解答学员的问题。3.角色扮演:让学员扮演不同角色,模拟实际工作场景,锻炼他们的5S/6S管理能力。4.小组讨论:组织学员进行小组讨论,分享经验和解决问题,促进学员之间的互动和学习。5.实践操作:安排学员在实际工作中应用5S/6S管理,通过实践提高他们的技能和意识。5S/6S管理可以帮助工厂更好地管理物料和设备,减少损耗和维修成本。
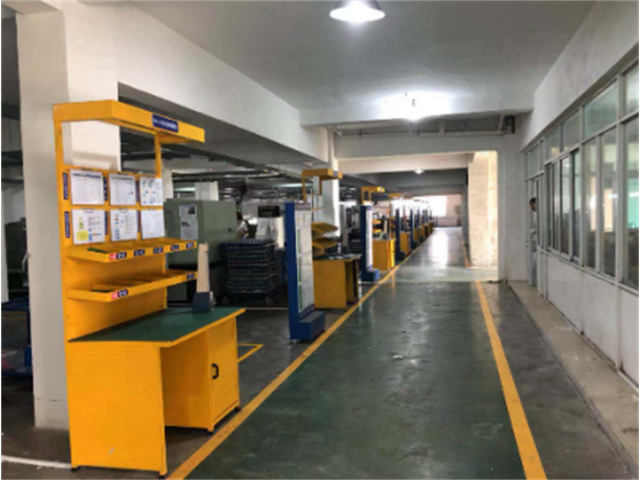
要确保5S/6S管理能够持续有效地执行,可以考虑以下几个方面:1.建立明确的目标和标准:确定5S/6S管理的目标和标准,确保所有员工都清楚地了解要达到的标准,并且明确自己的责任和角色。2.提供培训和教育:为员工提供必要的培训和教育,使他们了解5S/6S管理的原理、方法和技巧,并掌握相关的知识和技能。3.建立持续改进的机制:建立一个持续改进的机制,鼓励员工提出改进意见和建议,并及时跟进和实施这些改进措施。4.设立奖励和激励机制:设立奖励和激励机制,鼓励员工积极参与5S/6S管理,并认可他们的贡献和成绩。5.定期检查和评估:定期检查和评估5S/6S管理的执行情况,发现问题和不足,并及时采取纠正措施,确保管理的持续有效性。6.建立文化和氛围:营造一个积极的工作文化和氛围,让员工乐于参与5S/6S管理,并将其视为日常工作的一部分。通过5S/6S管理,工厂可以提高员工的工作环境,创造一个安全、整洁、舒适的工作场所。工厂5S/6S培训多少钱
通过5S/6S管理,工厂可以提高员工的安全意识和工作环境的安全性,减少事故发生的可能性。车间5S/6S
评估5S/6S精细化管理的实施效果并进行持续改进可以采取以下步骤:1.设定目标和指标:明确5S/6S管理的目标,并制定相应的指标来衡量实施效果。例如,可以设定减少浪费、提高工作效率、改善工作环境等指标。2.收集数据:收集与指标相关的数据,可以通过观察、记录、问卷调查等方式获取数据。例如,可以记录工作站点的整洁度、工作流程的改进情况、员工的反馈等。3.分析数据:对收集到的数据进行分析,找出问题和改进的机会。比较实际情况与设定的目标和指标,识别差距和潜在问题。4.制定改进计划:根据分析结果,制定具体的改进计划。确定需要采取的措施和行动,明确责任人和时间表。5.实施改进计划:执行改进计划,并确保相关措施得到有效实施。监督和跟踪改进计划的进展,确保按计划进行。6.评估改进效果:对改进措施的效果进行评估。比较改进前后的数据,评估改进的程度和效果。可以使用各种评估方法,如对比分析、统计分析、员工满意度调查等。7.持续改进:根据评估结果,进一步优化和改进5S/6S管理。根据实际情况调整目标和指标,并制定新的改进计划。持续监督和改进,确保管理效果的持续提升。车间5S/6S
上一篇: 浙江注塑工厂精益生产管理咨询公司
下一篇: 苏州厂区5S/6S服务费用