大朗音箱模具设计
高速切削技术对机床的性能要求很高。机床需要具备高转速的主轴、快速的进给系统和高精度的控制系统。主轴转速通常可以达到每分钟数万转甚至更高,这样可以保证刀具在高速旋转下的切削稳定性。同时,进给系统要能够实现快速准确的位移,以满足高速切削的进给要求。在控制系统方面,要能够精确控制刀具的运动轨迹和切削参数,保证加工精度。对于刀具而言,高速切削需要使用专门的高速刀具。这些刀具通常采用先进的涂层技术和特殊的刀具几何形状,以适应高速切削时的高温、高压环境。在加工过程中,高速切削产生的热量大部分被切屑带走,减少了对模具材料的热影响,从而提高了模具的加工质量,特别是在加工高硬度的模具材料时,高速切削技术的优势更加明显。模具的应用不仅限于传统的制造领域,还逐渐拓展到新能源、航空航天等新兴领域。大朗音箱模具设计
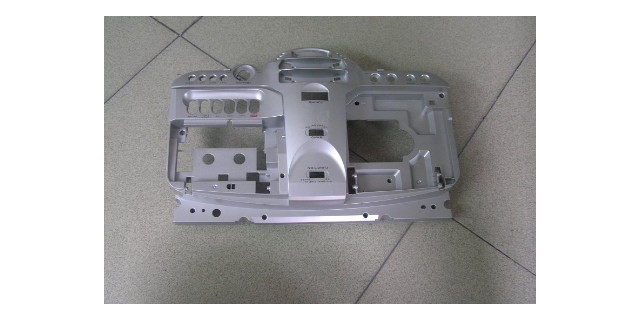
模具在制造业中扮演着举足轻重的角色。首先,模具可以提高生产效率。通过模具的复制性生产,可以快速、准确地生产出大量相同的产品,满足市场需求。其次,模具可以降低生产成本。模具的使用可以减少人工操作和材料浪费,降低生产成本。此外,模具还可以提高产品质量。模具的精密制造可以确保产品的尺寸和形状的一致性,提高产品的质量。随着制造业的不断发展,模具技术也在不断进步。一方面,模具的设计和制造技术越来越智能化和数字化。通过引入先进的CAD/CAE/CAM技术和人工智能等技术手段,可以实现模具的快速设计和精确制造。另一方面,模具的材料和热处理技术也在不断创新。新型模具材料和先进的热处理技术可以提高模具的硬度和耐磨性,延长其使用寿命。总之,模具作为制造业的精密之器,其设计和制造技术的不断提高将推动制造业向更高水平发展。未来,随着新材料、新工艺和新技术的不断涌现,模具将在制造业中发挥更加重要的作用。东坑音响模具定作模具的创新设计能够为企业带来更高的生产效率和更低的成本。
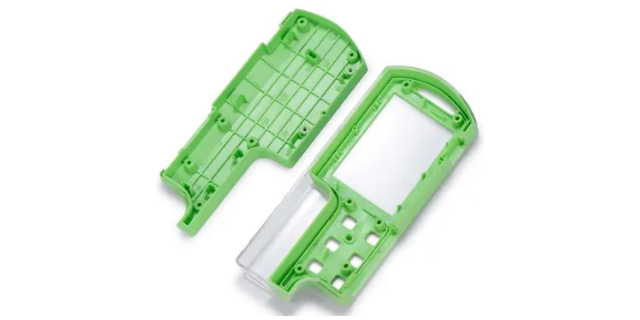
模具加工的数控编程基础。在模具加工中,数控编程是实现精确加工的关键环节。数控编程首先要对模具的三维模型进行详细分析,了解各个加工面的形状、尺寸和精度要求。例如,对于模具型腔中的复杂曲面,要确定合适的加工策略,如采用等高线加工、环绕等距加工等。选择合适的刀具是数控编程的重要内容。刀具的类型、直径、长度和材质都要根据加工部位的特点来选择。在加工模具的深腔部位时,需要选择长径比合适的刀具,以保证刀具的刚性和加工精度。对于硬度较高的模具材料,要使用硬质合金刀具或涂层刀具,提高刀具的耐磨性。
模具加工,质量控制的关键环节。模具加工的质量直接关系到模具的使用寿命和产品的质量。在加工过程中,需要从原材料的选择开始严格把关。质量的原材料可以保证模具的强度和耐磨性。然后,在每一道加工工序中,都要进行严格的尺寸测量和表面质量检测。例如,采用三坐标测量仪对模具零件的尺寸进行精确测量,确保其符合设计要求。同时,对模具表面进行抛光处理,提高表面光洁度,减少产品成型时的摩擦阻力。此外,还需要进行模具的试模和调试,及时发现和解决可能存在的问题。通过严格的质量控制,才能生产出高质量的模具,为产品的生产提供可靠保障。环境检测有助于监测环境政策的执行情况,为政策执行力的提升提供依据。
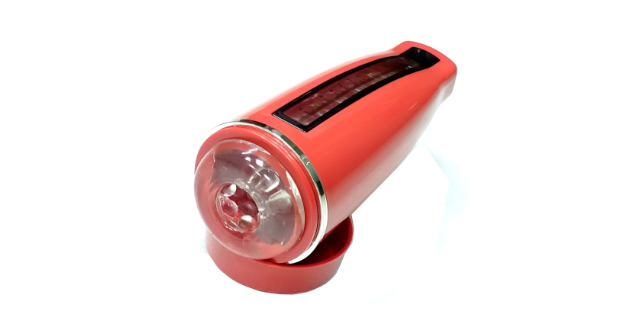
随着科技的不断进步和工业的不断发展,模具技术也在不断创新和进步。未来模具技术的发展趋势将主要体现在以下几个方面:数字化设计:利用计算机辅助设计软件进行模具设计已成为主流趋势。数字化设计技术可以提高模具设计的效率和精度减少设计过程中的错误和修正成本。精密加工技术:随着精密加工技术的不断发展模具的制造精度将进一步提高。新型加工设备和技术的应用将使得模具的制造更加高效、精细。智能化制造:智能制造和工业互联网的兴起将为模具制造行业带来新的发展机遇。通过引入智能化设备和系统模具制造过程可以实现自动化、智能化和柔性化进一步提高生产效率和产品质量。新材料应用:随着材料科学的发展新型材料的应用将为模具设计提供更多选择。新材料的应用可以改善模具的耐磨性、耐腐蚀性和导热性能从而提高模具的寿命和生产效果。模具的多样化设计能够满足不同客户的个性化需求。常平铝压铸模具批量定制
模具能够精确控制产品的成型压力,保证了产品的结构稳定性。大朗音箱模具设计
对于高硬度的模具材料,如硬质合金模具,电火花加工不受材料硬度的限制,可以有效地加工出所需的形状。电极的制作是电火花加工的关键环节。电极材料通常选择铜或石墨,根据加工部位的精度和形状要求来确定。电极的形状和尺寸要根据模具的设计精确制作,因为电极的精度直接影响加工后的模具精度。在电火花加工过程中,要合理设置放电参数,如放电电流、放电时间、脉冲间隔等,这些参数影响着加工速度和表面质量。同时,要注意加工过程中的排屑问题,良好的排屑可以提高加工效率和质量,防止出现电弧烧伤等缺陷。大朗音箱模具设计
上一篇: 深圳电子锁模具定做
下一篇: 金属包胶射出批量定制