中山模具设计加工
国模具工业的发展历史可以追溯到上世纪50年代,当时主要依附于企业的一个配件加工车间,模具制造企业较少且产量低。1953年,长春汽车制造厂建立了中国较早冲模车间,标志着中国模具工业的开始。随后,随着项重点工程的开工,陆续派人前去其他国家学习模具设计与制造。1962年,成立了我国家专业模具生产厂,为了适应模具生产发展的需要,颁布了我国模具标准。380年代初期至90年代中期,中国开始实行开放政策,国内模具制造企业开始引进国外先进生产设备和科学管理理念,并自行研制开发了一批适合我国国情的模具新钢种。90年代以来,民营的模具厂崛起,数控机床的大量引进,CAD、CAE、CAM的逐步实施,模具行业蓬勃发展,中国一跃成为模具制造大国。然而,尽管中国模具工业取得了的发展,模具市场仍存在一定差距,主要依赖进口。未来,随着技术的不断进步和市场的不断扩大,中国模具工业有望进一步缩小与国际先进水平的差距,实现从模具大国到模具强国的转变模具工业生产上用以注塑、吹塑、挤出、压铸或锻压成型、冶炼、冲压等方法得到所需产品的各种模子和工具。中山模具设计加工
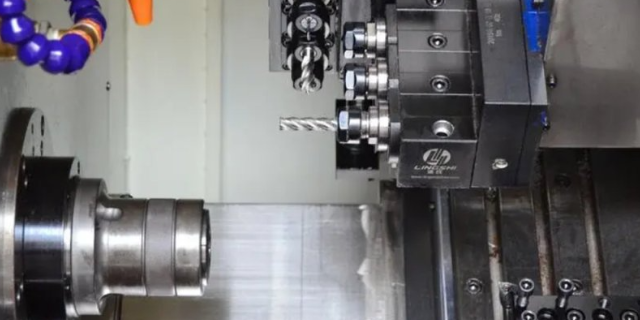
无流道凝料模具是针对热塑性胶料,利用加热或隔热的方法使流道内的胶料始终保持熔融状态,从而达到无流道凝料或少流道凝料目的的注射模具。优点:1.无流道凝料或少流道凝料,胶料的有效利用率高,并可充分发挥注射机的塑化能力。2.熔融胶料在流道里的压力损耗小,易于充满型腔及补缩,可避免产生胶件凹陷、缩孔和变形。3.缩短了成形周期,提高了生产效率。4.浇口可自动切断,提高了自动化程度。5.能降低注射压力,可减小锁模吨位。缺点:1.装有热流道板的模具其闭合高度加大,有可能需要选用较大的注射机。2.热唧咀、热流道板中的热量经热辐射和热传导影响前模温度,模具设计时应尽量减少热传递,加强前模冷却。3.模具成本较高中山模具设计加工气辅模具及适应注射成型等工艺的模具将有较大发展。
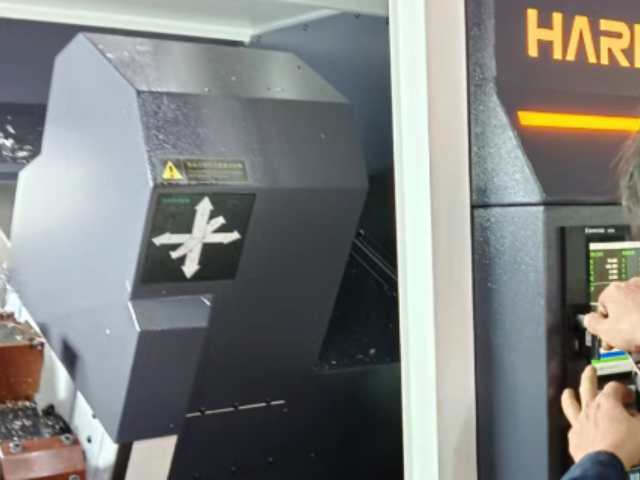
熟悉数控车床的加工工艺和加工参数。不同的工件需要采用不同的加工工艺和加工参数,需要根据实际情况进行选择和调整。学习数控车床的加工工艺和加工参数,包括切削速度、进给速度、切削深度等参数的设置和调整方法,以及如何进行精确的加工操作。此外,注重实践操作和经验积累。掌握数控车床需要不断地进行实践操作,通过实际的加工过程来积累经验。在实际操作中,需要注意观察加工情况,及时发现和解决问题,不断总结和积累经验,逐步提高自己的操作技能和水平。
注塑零件在脱模时需要克服零件与模具的摩擦力,要克服大气压力(一些半封闭的壳、筒类零件),还要克服模具机构本身之间的摩擦力。因此为了克服脱模力,保证注塑模具稳定工作,诞生了很多精巧的脱模机构。这些机构按推出动作的动力源分类可分为:手动脱模、机动脱模、液压与气动脱模。按推出动作特点分类双脱模可分为:一次脱模、二次脱模、顺序脱模、浇注系统凝料脱模、带螺纹塑件脱模。CNC数控编程培训、车铣复合培训、浮雕技术培训、三轴和五轴机技术培训、UG产品设计培训推动制造业进步。模具行业的技术密集、劳动密集特点,促进了制造业的技术创新和转型升级。
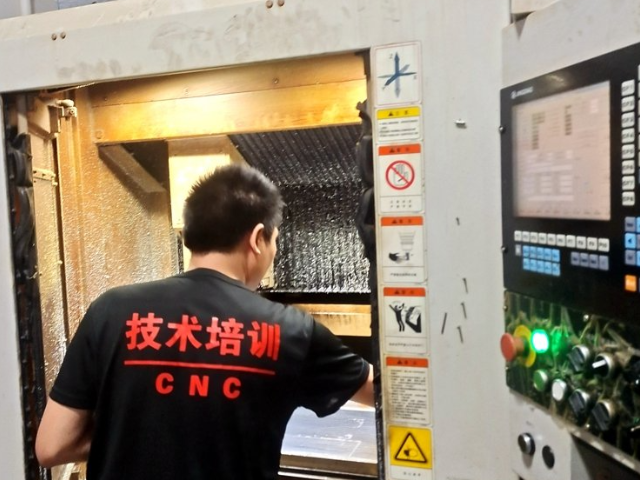
热流道模具:此类模具结构与细水口大体相同,其比较大区别是流道处于一个或多个有恒温的热流道板及热唧嘴里,无冷料脱模,流道及浇口直接在产品上,所以流道不需要脱模,此系统又称为无水口系统,可节省原材料,适用于原材料较贵、制品要求较高的情况,设计及加工困难,模具成本高。热流道系统,又称热浇道系统,主要由热浇口套,热浇道板,温控电箱构成。我们常见的热流道系统有单点热浇口和多点热浇口二种形式。单点热浇口是用单一热浇口套直接把熔融塑料射入型腔,它适用单一腔单一浇口的塑料模具;多点热浇口是通过热浇道板把熔融料分枝到各分热浇口套中再进入到型腔,它适用于单腔多点入料或多腔模具。CNC数控编程培训、车铣复合培训、浮雕技术培训、三轴和五轴机技术培训、UG产品设计培训机械制图:这是模具设计的基本技能,需要掌握投影定律、三视图投影等。潮州塑料模具设计供应
市场大:模具设计是工业之母,市场需求大,每年市场百万人才需求。中山模具设计加工
CNC电脑锣操机与模具设计的结合CNC电脑锣操机和模具设计,在现代制造业中往往是密不可分的。模具的复杂结构和高精度要求,使得CNC电脑锣操机成为其加工的设备。而模具设计的精确性和高效性,也为CNC电脑锣操机的加工提供了有力的保障。两者的完美结合,为现代制造业带来了前所未有的发展机遇。总结CNC电脑锣操机和模具设计作为现代制造业的两大支柱,为制造业的发展提供了强大的技术支持。随着技术的不断进步和应用领域的不断拓展,它们在未来制造业中的地位将更加重要。我们有理由相信,在CNC电脑锣操机和模具设计的共同推动下,现代制造业将迎来更加美好的明天。 中山模具设计加工
上一篇: 潮州专业的数控培训
下一篇: 广州汽车覆盖件模具设计