压力管道制造
管道焊接(四)
7安装Ⅱ形或Ω形膨胀弯管,应符合下列规定:
1)按设计规定值进行预拉伸或预压缩。
2)水平安装时,平行臂应与管线的坡度相同,两垂直臂应平行。
3)铅垂安装时应设置排气及疏水装置。
8管道的安装(包括定位和与管道组成件的联接)应符合下列要求:
1)严格按照设计规定的位置、型式、数量设置管道的全部管架。
2)锚固型管架应在管道预予拉伸(压缩)前固紧;导向型或滑动型支架其相对移动面应平滑,不得有卡涩现象,滑移方向和定位提前量正确。
3)弹簧管架的弹簧活动部分应锁住,待管道试压、防腐、保温完毕后方可解锁,并按设计负荷值整定弹簧的负荷。
4)不容许管道的碳钢部件直接接触的管道组成件(例如其材质为不锈钢或部分有色金属),应在它们的接触部位之间垫以隔离物,所有隔离物应既能长期耐受管道组成件的外壁温度和工作负荷,亦不会对其造成二次污染。 管道由管子、管件、法兰、螺栓连接、垫片、阀门、其他组成件或受压部件和支承件组成的装配总成。压力管道制造
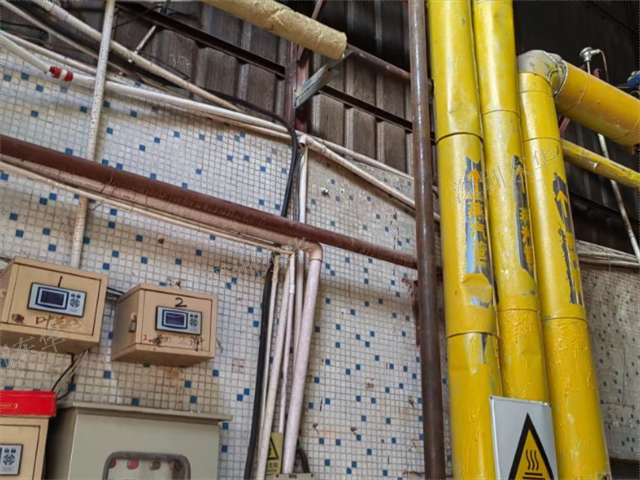
压力管道的焊缝设置
管道(夹套管除外)焊缝的设置应避开应力集中区,且应符合以下规定:
a)当公称直径大于或等于150mm时,直管段上两对接环焊缝中心面之间的距离应不小于150mm;当公称直径小于150mm时,该距离应不小于管子外径。
b)管道环焊缝距离弯管(不包括弯头)起弯点的距离应不小于100mm,且不得小于管子外径。
c)管道环焊缝与支吊架的净距离应不小于50mm。需要热处理的焊缝与支吊架的距离应不小于焊缝宽度的5倍,且不得小于100mm。
d)不宜在焊缝及其边缘上开孔。当无法避免在焊缝上开孔或开孔补强时,应对以开孔中心为中心、在1.5倍开孔直径或补强板直径范围内的焊缝进行无损检测,检测合格后方可进行开孔。补强板覆盖的焊缝应磨平。 广州广东压力管道我们采用优良材料和先进设备,结合严格的质量控制流程,以确保每一项工程都能达到满意的质量标准。
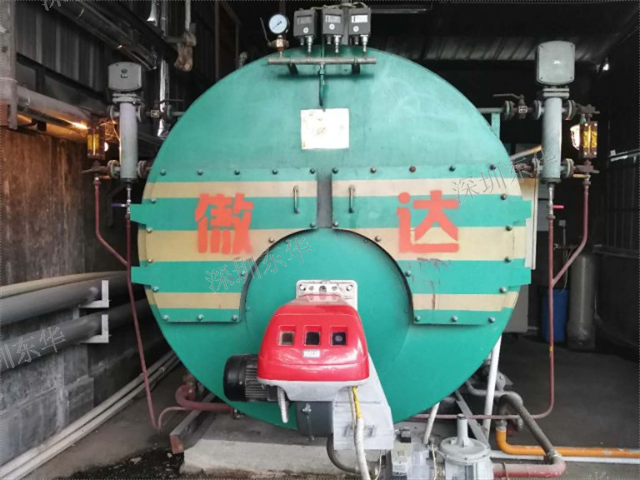
管道安装(五)
8管道的检验和试验
1)管道施焊完毕后,应由施焊焊工对其进行外观检查,由焊接质量检查人员进行抽查。焊缝外观应成形良好,焊波均匀,环焊缝能盖起坡口2mm左右,且平缓过渡到母材;角焊缝的焊脚高度符合设计或规范的要求。焊缝的表面质量应符合GB/T20801《压力管道规范工业管道》等标准的相应要求。
2)需进行焊后处理的焊缝,应抽查焊缝及热影响区的硬度值(沿测量区圆周取两测点测取的平均值),碳素钢不得超过母材的120%;合金钢不宜超过母材的125%。抽查数量不应少于热处理焊口总数的10%。抽检不合格者,按不合格数量加倍抽检,且对不合格的焊缝重新做热处理。若总抽检数有接近50%不合格,侧视该热处理工艺为不符合要求,应重新编订,再行热处理。
压力管道保温如何进行成品保护
1管道及设备的保温,必须在地沟及管井内已进行清理,不再有下落不明道工序损坏保温层的前提下,方可进行保温。
2一般管道保温应在水压试验合格,防腐已完方可施工,不能颠倒工序。
3保温材料进入现场不得雨淋或存放在潮湿场所。
4保温后留下的碎料,应由负责施工的班组自行清理。
5明装管道的保温,土建若喷浆在后,应有防止污染保温层的措施。
6如有特殊情况需拆下保温层进行管道处理或其它工种在施工中损坏保温层时,应及时按原要求进行修复。 压力管道范围规定为工作压力大于或者等于0.1MPa(表压)。
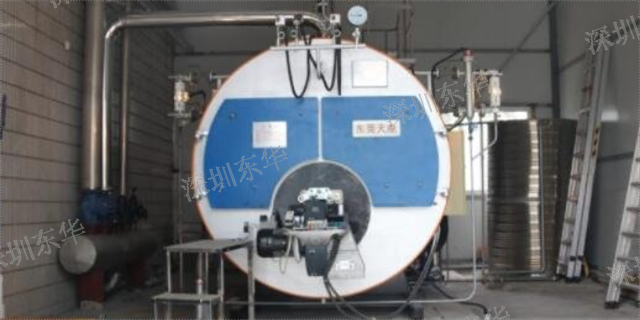
管道的预制工作应按设计单位提供的管道系统单线图进行,在现场的预制加工间或后方的加工厂内,根据施工图纸把所需的管道集中加工预制、排列编号后运往现场安装。管道预制应遵守下列程序和规定:
1管道组成件应按单线图规定的数量、规格、材质选配,并按单线图表明管线号和按预制的顺序表明每个组成件的顺序号。
2为了保证工程质量和便于安装,应合理选定自由管段和封闭管子段。
3自由管段按单线图长度加工,封闭管段应留用适当的裕量,按现场安装实测后的长度加工。
4预制管段应具有足够的刚性,必要时进行加固,以保证在存放、运输过程中不变形。
5预制完毕的管道,应将内部清理干净,及时将管口封闭。
6预制管道运抵现场,经现场安装人员检查、确认合格后,方可交付安装。
7自由管段与封闭管段的加工尺寸偏差应符合规定。 管道组成件和管道支承件的种类繁多,各种材料各有特点和具体技术要求,材料选用复杂。压力管道 规范
我们的管道安装技术,让您的工作效率倍增。压力管道制造
管道系统的吹扫与清洗
1管道在压力试验合格后,建设单位应负责组织系统吹扫与清洗(简称吹洗)工作,并应在吹洗前编制吹洗方案。
2设备运行前,需要对其安装检验合格后的管道和设备进行吹扫和清洗,目的是通过使用空气(氮气)、蒸汽、水及化学溶液等流体,进行吹扫和冲洗,去除施工过程中的残留杂质,保证装置顺利运行。
3吹洗工作应按生产工艺流程,按系统进行。吹洗应包括下列内容:
1)管道系统的人工清扫和水冲洗。
2)管道系统的化学清洗和预膜处理。
3)蒸汽管道系统的蒸汽吹扫。
4)工艺管道系统的空气吹扫。
压力管道制造
上一篇: 广州蒸汽锅炉询问报价
下一篇: 玻璃钢压力管厂家