福建工厂精益改善
技术创新:随着科技的不断发展,企业需要不断地进行技术创新,以适应市场的变化和客户的需求。精益改善也需要与技术创新相结合,例如采用自动化、智能化等技术手段,提高生产效率和质量。应对突发事件:精益文献中对突发事件和变革的关注较少,但企业在实际运营中可能会面临各种突发事件,如自然灾害、市场变化等。企业需要建立应急预案,提高应对突发事件的能力。同时,企业也应该在精益改善过程中考虑到突发事件的影响,制定相应的应对措施。降低生产过程中的次品率,从而节省了因次品而浪费的生产时间。福建工厂精益改善
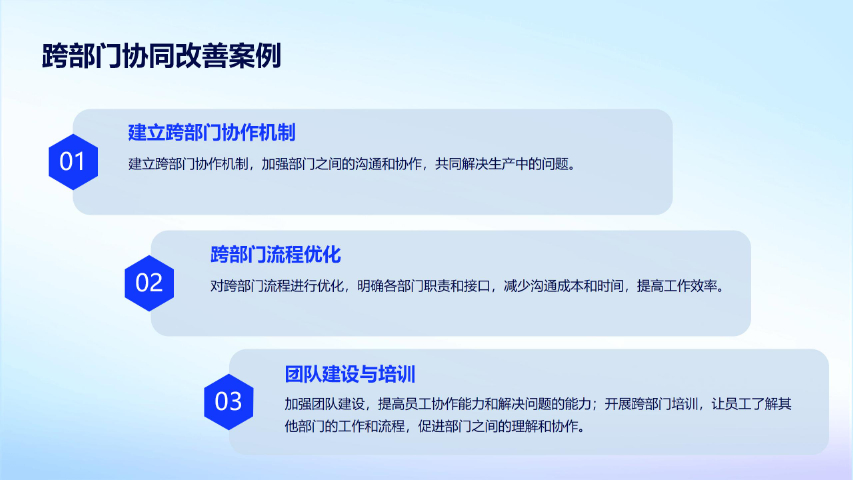
汽车市场竞争激烈,该企业面临着生产成本高、生产周期长等问题,需要对生产流程进行优化,以提高竞争力。优化措施:价值流分析与浪费消除:通过价值流分析,企业发现生产线上存在大量的库存积压和等待时间。于是,引入了准时化生产(JIT)模式,根据客户订单需求来拉动生产,减少了中间库存。例如,与零部件供应商建立紧密的合作关系,要求供应商按照生产进度及时供货,而不是提前大量囤货。生产线布局调整:重新调整了生产线布局,将一些关联性强的工序设置在相邻位置,减少了零部件在车间内的搬运距离。例如,将发动机组装和汽车底盘组装工序安排在相邻区域,方便零部件的传递和组装。浙江管理精益改善方法优化质量改进流程,提高质量改进的效率。
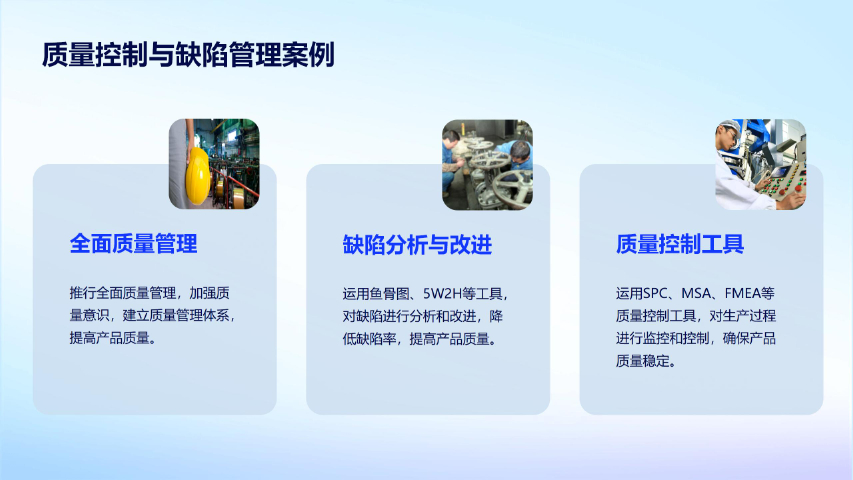
沟通与培训:向所有涉及优化流程的人员详细介绍优化方案的内容、目的和实施步骤。对他们进行必要的培训,使他们能够熟悉新的流程和操作方法。例如,在实施新的财务报销流程时,要对员工进行报销软件使用的培训。小范围试点:对于复杂的优化方案,可以先在小范围内进行试点。例如,在企业的多个部门中,选择一个部门先试行新的绩效考核流程,观察效果并收集反馈。***实施:在试点成功的基础上,逐步在整个范围内实施优化后的流程。在实施过程中,要密切关注流程的运行情况,及时解决出现的问题。
精益改善是一种以消除浪费、提高效率和质量、降低成本为目标,通过持续不断地对企业的生产、管理、流程等各个环节进行优化和改进的管理理念和方法。以下是其详细介绍:主要原则价值原则:强调从客户的角度出发,识别和确定产品或服务的价值,将所有活动都聚焦于为客户创造价值,去除那些不增加价值的环节和流程。价值流原则:对整个价值流进行***的分析和优化,包括从原材料采购到产品交付给客户的全部过程,打破部门之间的壁垒,实现流程的顺畅和高效。流动原则:致力于使价值流中的各个环节能够快速、顺畅地流动,减少中间的停顿、等待和库存积压,通过优化布局、减少批量、同步生产等方式实现生产的连续流动。建立质量预防体系,提前发现质量隐患。
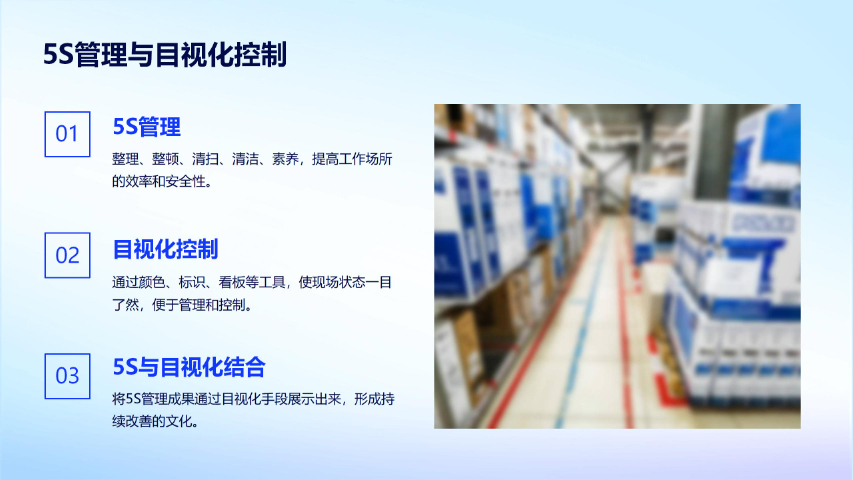
去除冗余环节:根据流程分析的结果,取消那些没有价值的环节。例如,在会议组织流程中,如果会前通知已经通过电子邮件发送,就可以取消电话通知这个重复的环节。整合流程步骤:将一些分散的、关联性强的环节进行合并。例如,在产品设计和开发流程中,将概念设计和初步设计阶段的部分评审环节合并,以减少评审次数,提高效率。调整流程顺序:合理调整环节的先后顺序,使流程更加顺畅。例如,在企业的新员工入职流程中,先进行入职培训,再分配工作任务,可能比先分配任务再培训更有利于新员工快速适应工作。引入新技术或方法:利用信息技术、自动化设备或先进的管理方法来优化流程。例如,在仓库管理流程中,引入自动化仓储系统和库存管理软件,可以提高库存盘点和货物出入库的效率。建立学习型组织:企业持续进行精益改善,需要不断学习和吸收新的知识和方法。精益改善流程
改善生产信息传递的及时性和准确性,减少因信息不畅导致的效率损失。福建工厂精益改善
建立评估指标体系:根据优化的目标,确定评估指标,如效率指标(流程周期缩短率、单位时间产出增加率)、质量指标(产品合格率提升率、客户投诉减少率)、成本指标(成本降低率)等。定期评估:按照一定的周期(如每月或每季度)对优化后的流程进行评估。通过对比优化前后的数据,分析优化效果。例如,通过比较优化前后的生产周期,计算生产周期缩短的百分比。持续改进:根据评估结果,对于未达到预期效果的部分,分析原因并进行调整。同时,随着企业内外部环境的变化,要不断寻找新的优化机会,对流程进行持续改进。例如,当市场需求发生变化或新技术出现时,及时调整产品生产流程以适应新的情况。福建工厂精益改善
上一篇: 宁波业务精益改善有什么成效
下一篇: 温州精益改善方法