北京工业半导体治具
半导体封装石墨模具的高硬度是因为在微观组织结构上它是由金刚石和石墨混合而成,金刚石成分决定了它具有高硬度。半导体封装石墨模具的另一特性是它的原子结构排布紧密,不象其它涂层内部微观结构中有较多空隙和缺陷,加上由于主要成分为碳,半导体封装石墨模具涂层的化学稳定性,在防腐和防止材料粘黏等应用上有良好的效果。半导体封装石墨模具涂层是采用离子束技术通过将碳氢化合物气体离子而生成的一种含氢类金刚石涂层。由于其结构中含有较多的金刚石成分,其薄膜硬度比由其它技术,如此控溅射或离子增强型化学气相沉积而获得的半导体封装石墨模具更高。不同类型的治具适用于不同的生产环节,需要根据生产需求进行合理选择。北京工业半导体治具
半导体治具
在材料选择过程中,还需考虑材料的热膨胀系数、弹性模量等物理性能,以确保治具在高温、高压等恶劣环境下仍能保持稳定性能。此外,材料的成本也是需要考虑的因素之一,需要在满足性能要求的前提下尽可能降低材料成本。加工技术半导体治具的加工技术是实现其高精度、高质量的关键。常用的加工技术包括数控加工、电火花加工、激光加工以及精密磨削等。数控加工技术能够实现治具的自动化、高效化生产,提高加工精度和效率;电火花加工技术适用于加工复杂形状和难以用传统方法加工的治具;激光加工技术则具有高精度、高效率、无接触等优点,适用于加工高精度要求的治具;精密磨削技术则能够进一步提高治具的表面质量和精度。在加工过程中,还需严格控制加工参数,如切削速度、进给量、切削深度等,以确保加工质量和效率。同时,对于特殊形状的治具,还需采用特殊的夹具和工装,以确保加工过程中的稳定性和精度。北京工业半导体治具半导体治具需要具备高精度和高稳定性的特点,以保证半导体芯片的位置和稳定性。
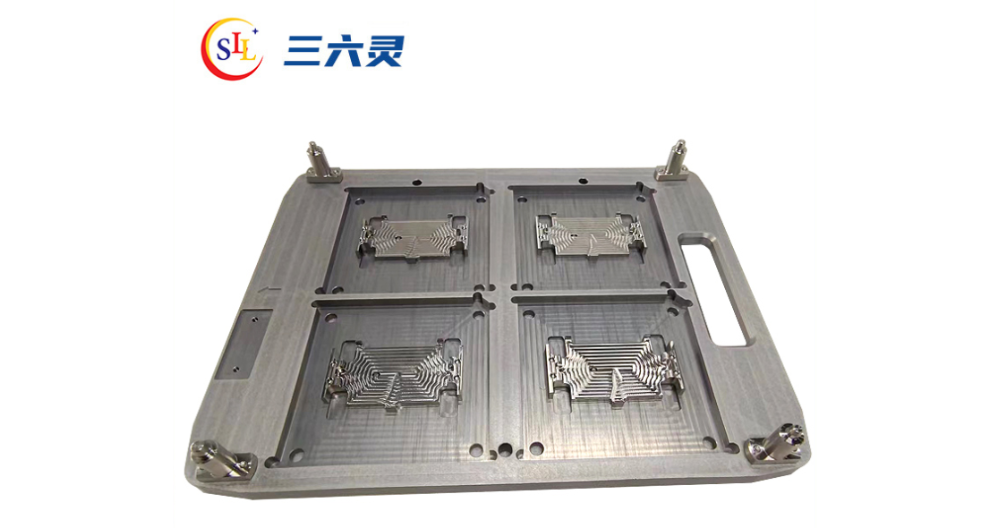
维护与挑战半导体治具的维护对于保障其精度和延长使用寿命至关重要。由于治具经常暴露在严苛的生产环境中,需要定期进行清洁、检测和维护。然而,随着半导体制程技术的不断进步,治具的设计和制造也面临着更大的挑战,如何快速适应新技术和提升自身精度是当前治具发展的关键。未来发展趋势未来,随着半导体行业的持续发展,对治具技术的需求将更加复杂和精细。新型材料的应用、智能制造技术的融合、更高标准的精密度要求将是治具技术发展的趋势。同时,随着3DIC技术的发展,治具的设计和制造也将步入一个新的发展阶段。结论:半导体治具在现代半导体行业中发挥着不可替代的作用。通过不断的技术创新和优化,治具技术正推动着半导体制造业的精密化和高效化。面对未来的挑战,持续的技术升级和应用拓展将是保持竞争力的关键。随着全球半导体市场的扩大,治具技术的进步将为整个行业的发展带来新的机遇。
半导体治具的制造工艺半导体治具的制造工艺主要包括以下步骤:1.设计:根据客户需求和实际应用场景,进行治具的设计和方案制定。2.材料准备:选择合适的材料,如高精度钢材、陶瓷材料等,准备进行治具的制造。3.加工:利用数控机床等精密设备,进行治具的加工和制造。4.表面处理:对治具的表面进行抛光、镀膜等处理,以提高其精度和使用寿命。5.检测:对制造完成的治具进行精度和性能检测,确保其符合要求。6.包装:对合格的治具进行包装,以保护其在使用过程中的安全性和稳定性。这些治具对于确保半导体设备的产量和质量都至关重要。
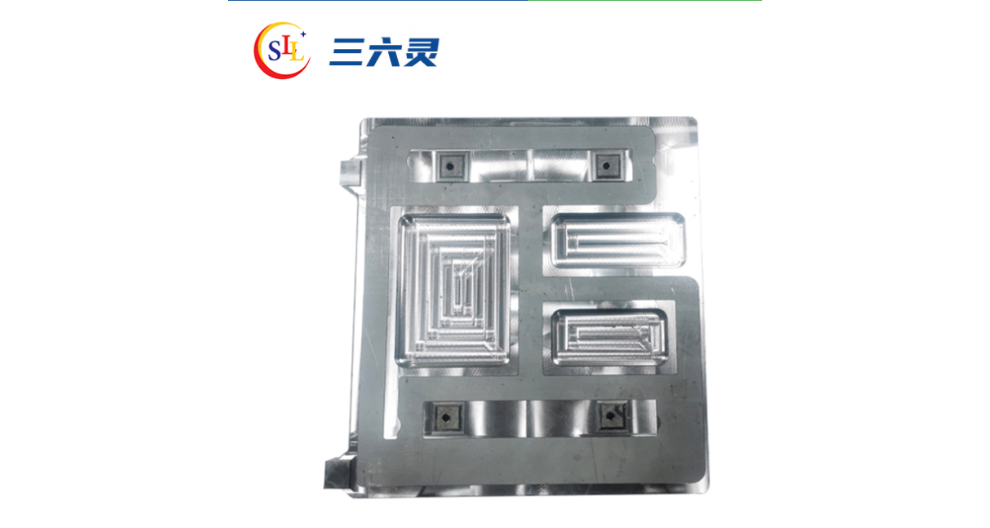
模块化与标准化:为了便于半导体制造设备的维护和升级,半导体治具将越来越趋向于模块化和标准化设计。这不仅可以降低了制造成本和缩短研发周期,还可以提高设备的兼容性和可扩展性。绿色环保:随着环保意识的提高和绿色制造的要求,半导体治具将更加注重环保性能。未来,半导体治具将采用环保材料、优化制造工艺、降低能耗和减少废弃物排放,以实现绿色制造和可持续发展。综上所述,半导体治具在半导体制造过程中发挥着举足轻重的作用。随着半导体技术的不断进步和应用领域的不断拓展,半导体治具将继续发展创新,为半导体产业的快速发展提供有力支撑。半导体治具的设计和制造需要遵循严格的工艺流程和标准,以确保其质量和精度。北京工业半导体治具
半导体治具是现代电子制造中不可或缺的一部分,对于推动科技进步和产业发展具有重要作用。北京工业半导体治具
半导体治具的种类半导体治具种类繁多,根据用途和功能的不同,可分为以下几类:晶圆夹具:用于固定晶圆在制造设备中进行切割、研磨、抛光等工艺操作。晶圆夹具要求具有高精度、高稳定性和良好的热传导性能,以确保晶圆加工的质量和效率。芯片夹具:用于在封装过程中将芯片固定在封装基板上,确保芯片与基板之间的准确对接和稳定连接。芯片夹具需具备高可靠性、低应力以及良好的热膨胀性能,以适应封装过程中的温度变化和机械应力。测试夹具:用于在测试阶段将半导体器件固定在测试设备上,以便进行性能检测和质量评估。测试夹具要求具有快速定位、准确夹持和易于操作的特点,以提高测试效率和降低测试成本。北京工业半导体治具
上一篇: 南通精密半导体治具价格
下一篇: 昆山半导体石墨治具表面处理