江西FMEA七步法
FMEA 及其它活动的商业目标,如下: 1.提高汽车产品的质量、可靠性、可制造性、可服务性和安全性·确保获取各组件、系统和车辆之间的层次结构、连接、接口、级联和要求符合性信息 2.降低保修和商誉成本 在市场的激烈竞争中提高顾客满意度 3.证明产品和过程风险分析,从而为承担法律责任做好准备 4.减少开发过程中的后期变更 5.保持无缺陷产品的发布. 6.在内外部顾客和供应商之间进行有针对性的沟通 7.在公司内部建立知识库,即将获得的经验教训形成文件使组件、系统和车辆符合注册获批所需的法规。FMEA是一个组织的经验积累,为以后的设计开发项目提供了宝贵的参考。江西FMEA七步法
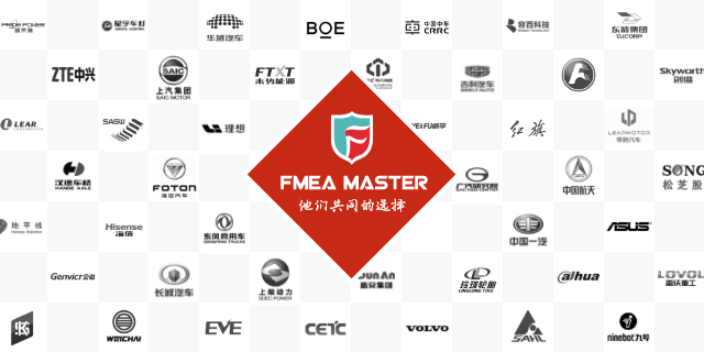
设计 FMEA (DFMEA) 是一科主要由设计责任工程师/团队使用的分析技术,用于确保在将零件交付生产之前,尽可能考虑并解决潜在失效模式及其相关失效起因或机理。 设计 FMEA 用于分析如块/边界图所示边界中所定义的系统、子系统或相关组件的功能,其内部要素之间的关系以及与系统边界外要素之间的关系。从而识别出可能存在的设计缺陷,将潜在的失效风险降低。系统设计 FMEA 由表示为系统要素 (项目) 的各种子系统和组件组成系统和子系统分析取决于视角或责任,系统提供整车层面的功能,这些功能通过子系统和组件级联。江西FMEA七步法FMEA,让企业质量更可靠。
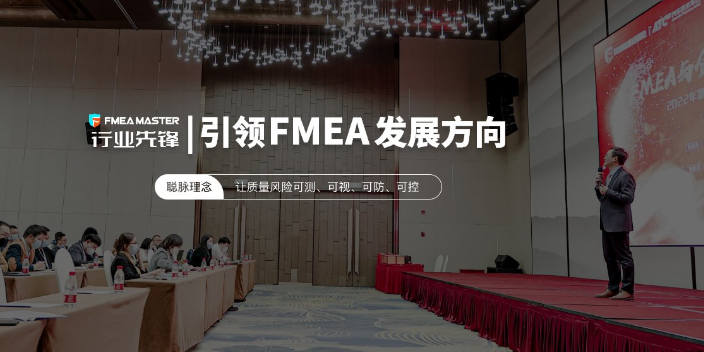
世界上开始采用FMEA这种概念与方法的是在20世纪60年代中期美国的航天工业。进入70年代,美国的海军相继应用推广这项技术,并制订了有关的标准70年代后期,FMEA被美国汽车工业界所引用,作为设计评审的一种工具。1993年2月美国三大公司联合编写了FMEA手册,并正式出版作为QS9000质量体系要求文件的参考手册之一,该手册于1995年2月出版了第2版。1994年,美国汽车工程师学会SAE发布了SAEJ1739一潜在失效模式及后果分析标准。 FMEA还被广泛应用于其他行业,如粮食、卫生、运输、燃气等部门。
FMEA(故障模式及影响分析)是一种系统性的分析方法,用于识别、评估和管理产品或过程中的潜在故障。 1. 团队合作 确保有一个多学科的团队,各成员能够提供不同的专业知识和经验。 促进团队成员之间的合作和交流,通过有效地沟通和讨论,提高分析结果的准确性。 2. 充分准备 在开始FMEA之前,收集和整理所有相关的信息和数据,包括产品或过程的设计、功能、材料等。 对相关标准、规范和先前的FMEA结果进行复查,确保有完整的背景知识。 FMEA是一个组织的经验积累,为以后的设计开发项目提供了宝贵的参考。FMEA还是识别特殊特性的重要工具。FMEA的结果也是用来制订质量控制计划。FMEA是可靠性的风险分析方法之一。
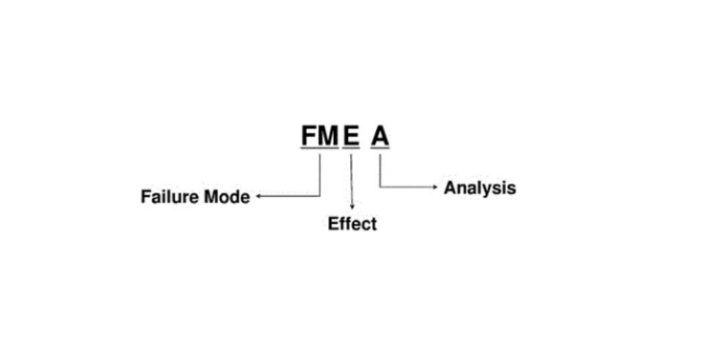
FMEA实际上意味着是事件发生之前的行为,并非事后补救。使用FMEA管理模式在早期确定项目中的风险,可以帮助电了设备制造商提高生产能力和效率,缩短产品的面市时间。此外通过这种模式也可使各类**对生产工艺从各个角度进行检测,从而对生产过程进行改进。所推荐的方案应该是正确的矫正,产生的效益相当可观。为了避免缺陷的产生,需要对工艺和设计进行更改。使用统计学的方法对生产工艺进行研究,并不断反馈给合适的人员,确保工艺的不断改进并避免缺陷产生。fmea失效分析五大工具。辽宁质量好的FMEA智能化
FMIEA管理记录的是一个不断努力的过程和连续性的工艺改进。江西FMEA七步法
FMEA认为,构成系统的所有零部件和元器件都不发生故障则整个导弹系统是可靠的,保证零部件和器件所含有的故障模式都不发生就能保证零部件和冗器件不发牛故障,从而保证系统的可靠性。因此,FMEA的根本任务就是对系统的故障模式进行控制,以满足系统的可靠性要求。但是,由于各种约束条件的限制,我们不可能找到系统所有的故障模式,也不可能保证找到的故障模式的发生概率为0.这样就需要进行故障影响分析和危害性分析,找到那些能够对系统产生较大危害性的故障模式,对这些故障模式实施有重点、有针对性的控制,使它们的故障发生概率在可接受的范围内,提高系统的可靠性。江西FMEA七步法
上一篇: 天津操作简单的FMEA咨询
下一篇: 广西新版FMEA培训