腔体加工费用
腔体加工是现代制造业中不可或缺的一环,它涉及在金属、陶瓷或复合材料等基体上,通过切削、铣削、钻孔、磨削等多种工艺手段,精确形成内部空腔结构的过程。这些空腔往往具有复杂的几何形状和高精度的尺寸要求,普遍应用于航空航天、医疗器械、半导体设备、精密仪器等领域。腔体加工不仅考验着机床的精度与稳定性,还依赖于先进的数控编程技术和材料科学的发展,是精密制造技术的集中体现。随着科技的进步,腔体加工技术也在不断创新。高速切削、五轴联动加工、微细加工等技术的应用,极大地提高了加工效率和精度。特别是激光加工、电火花加工等特种加工方法的引入,使得难以用传统机械加工方法实现的复杂腔体结构成为可能。此外,智能化、自动化技术的融合,如在线检测、自适应控制等,进一步提升了腔体加工的灵活性和可靠性,满足了市场对高质量、高效率加工产品的需求。在模具制造中,腔体加工的精度直接决定了产品的外观和质量。腔体加工费用
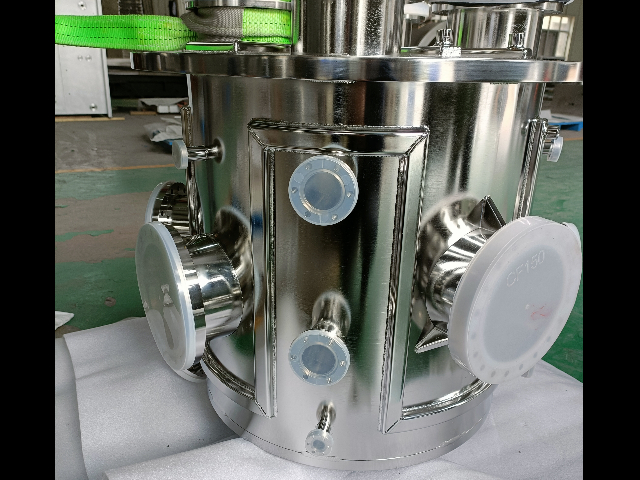
真空炉体的加工材料通常选用高纯度不锈钢、镍基合金或陶瓷等耐高温、耐腐蚀材料。这些材料的选择依据是它们能在极端条件下保持稳定性和耐用性。在加工工艺上,采用先进的数控铣削、精密焊接、电子束焊接及热处理等技术,以确保炉体结构的精确成型与强度高的连接。特别是针对复杂形状和精密尺寸的炉体部件,还需结合激光切割、数控弯管等特种工艺,以实现高精度加工与组装。真空炉体的密封性能是其能否有效维持炉内真空环境的关键。在加工过程中,需对炉门、法兰连接处等关键部位进行特殊处理,如采用高性能密封垫圈、双重密封结构等,以确保在高温高压下仍能保持优异的密封效果。此外,通过严格的泄漏检测与真空度测试,确保每一台真空炉体在出厂前均能达到设计要求的真空度标准,为材料处理提供稳定可靠的环境保障。腔体加工费用持续改进与创新,是腔体加工永恒的主题。
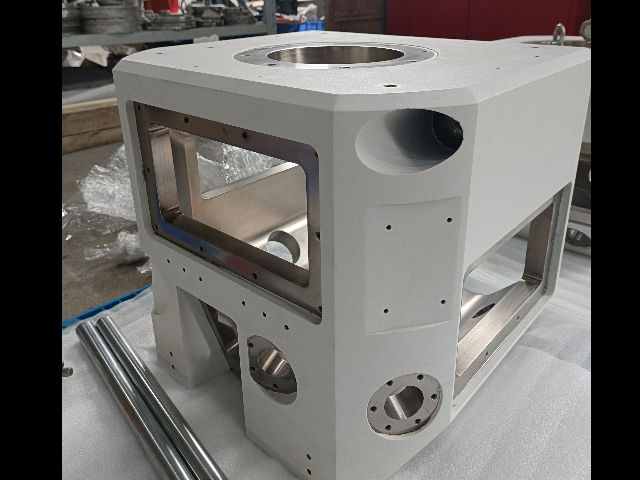
众所周知,在铝合金真空腔体加工完成后,还需进行一系列表面处理以增强其性能。一方面,通过阳极氧化处理在铝合金表面形成一层致密的氧化膜,提高耐磨性、耐腐蚀性和绝缘性。另一方面,针对等离子清洗机的特殊需求,可对腔体内壁进行特殊处理,如喷涂防粘涂层或进行微纳结构加工,以优化等离子体分布,提高清洗效率。此外,表面清洁度的控制也是不可忽视的一环,需采用超声波清洗、真空干燥等方法彻底去除加工过程中残留的油污、尘埃等杂质。
随着半导体技术的不断发展和市场需求的变化,半导体真空腔体加工正面临着越来越多的挑战和机遇。一方面,随着芯片制程的不断缩小和三维集成技术的发展,对真空腔体的加工精度和性能提出了更高的要求;另一方面,环保、节能和可持续发展的理念也促使着真空腔体加工技术的不断创新和优化。未来,半导体真空腔体加工将更加注重材料的选择与研发、加工技术的智能化和自动化、以及环保型加工技术的应用和推广。同时,还需要加强跨学科的合作与交流,共同推动半导体真空腔体加工技术的持续进步和发展。严格质量控制,确保腔体加工件一致性。
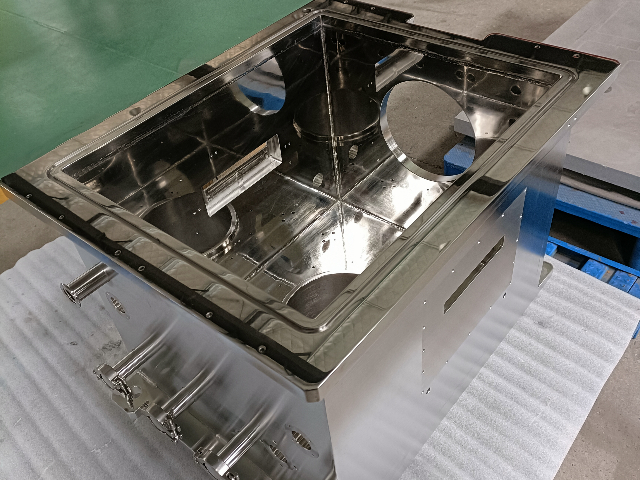
不锈钢真空腔体,作为现代工业与科研领域中的关键部件,以其良好的耐腐蚀性、强度高的及良好的密封性能,普遍应用于半导体制造、航空航天、材料科学研究及精密仪器制造等多个领域。其设计巧妙地将不锈钢材料的优良特性与真空环境的需求相结合,通过精密的加工技术,如数控铣削、焊接与表面处理,确保腔体内部达到极高的真空度要求,为各类精密实验和生产过程提供稳定可靠的环境条件。不锈钢真空腔体的加工涉及一系列复杂而精细的工艺步骤。首先,需要选用高纯度、低杂质的不锈钢材料作为基础,以保证腔体的整体质量和性能。随后,通过高精度的数控加工设备,对腔体进行轮廓切割、孔洞加工及内部结构的精细雕琢。尤为关键的是焊接工艺,需采用先进的真空焊接技术,确保焊缝的密封性同时避免对材料性能的影响。此外,表面处理如抛光、酸洗等也是必不可少的环节,以去除加工痕迹,提升腔体的表面光洁度和真空保持能力。在精密加工领域,腔体加工的技术水平是区分高低的标准之一。黑龙江D型真空腔体-2.1加工
环保材料应用,推动腔体加工绿色发展。腔体加工费用
半导体真空腔体的加工精度直接关系到其密封效果和内部环境的纯净度。因此,在机械加工阶段,需采用高精度数控机床、激光切割、电火花加工等先进技术,对腔体进行精细的切割、钻孔、铣削和研磨,确保各部件的尺寸精度和形状精度达到微米级甚至纳米级。同时,还需进行严格的尺寸检测和质量控制,以确保每个腔体都能满足设计要求。焊接是半导体真空腔体加工中的关键环节之一。为了确保腔体的气密性和强度,通常采用电子束焊接、激光焊接或真空钎焊等高级焊接技术。这些技术能够在保证焊接质量的同时,较大限度地减少焊接过程中产生的热应力和变形,从而保护腔体的整体性能和精度。此外,还需对焊接后的腔体进行严格的漏率检测和真空测试,以确保其达到预期的真空度和密封性能。腔体加工费用