浙江氮化丝锥板牙
为了满足不断变化的市场需求,钨钢丝锥也在不断创新和发展。一方面,制造商们在不断改进钨钢丝锥的制造工艺,提高其性能和质量。例如,采用先进的涂层技术和热处理工艺,增强丝锥的耐磨性和硬度。另一方面,研发人员也在不断推出新型的钨钢丝锥产品,以适应不同的加工需求。例如,针对特殊材料的加工需求,开发出的钨钢丝锥;为了提高加工效率,推出了多刃钨钢丝锥等。此外,随着数字化制造技术的发展,钨钢丝锥的设计和制造也越来越智能化。通过计算机辅助设计和制造技术,可以更加精确地控制丝锥的尺寸和形状,提高生产效率和质量。螺旋槽丝锥:用于孔深小于等于3D的盲孔加工,铁屑顺着螺旋槽排出,螺纹表面质量高。浙江氮化丝锥板牙
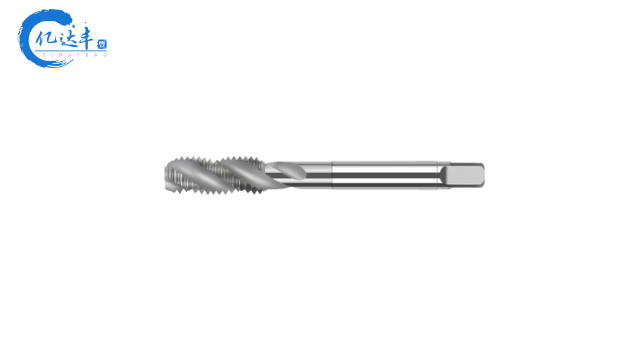
丝锥,恰似一位耐心的工匠,在金属的表面精心雕琢着细腻的螺纹。它安静地等待着工匠的操作,一旦启动,便以稳定而均匀的节奏开始工作。丝锥的刃口与金属相互作用,发出轻微而有节奏的摩擦声,仿佛在演奏一首工业的交响曲。在汽车零部件的制造中,丝锥发挥着重要作用。发动机内部的许多零件,如气缸盖、油底壳等,都需要通过丝锥加工出精确的螺纹,以确保密封和连接的可靠性。丝锥在这些关键部位的精细作业,直接关系到汽车发动机的性能和寿命。每一道螺纹的深度、螺距和表面质量,都经过了严格的控制和检测。在这个过程中,丝锥不仅是一种工具,更是保证汽车品质的关键因素之一。广州氮化丝锥型号丝锥的旋转速度和力度需要准确控制,否则容易损坏。
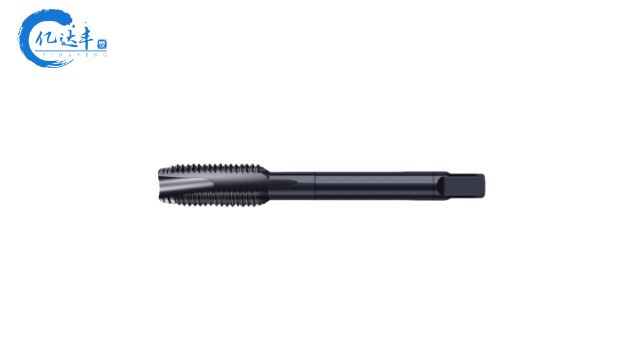
丝锥,如同一位默默耕耘的劳动者,在金属加工的领域里辛勤付出。它那朴实无华的外表下,隐藏着强大的功能。丝锥的设计充分考虑了力学原理和切削工艺,使得在加工螺纹时能够很大程度地减少阻力和磨损。在航空航天领域,丝锥的身影随处可见。飞机的结构件、发动机组件等,都对螺纹的精度和强度有着极高的要求。丝锥在这些关键部位的精确作业,为飞机的安全飞行提供了重要保障。由于航空航天材料的特殊性和复杂性,丝锥需要具备出色的耐高温、耐磨损和耐腐蚀性能。为了满足这些苛刻的要求,丝锥的制造采用了先进的材料和工艺,不断挑战着技术的极限。
丝锥,仿佛是一位执着的探险家,在金属的内部探寻着螺纹的奥秘。当它与金属相遇的那一刻,一场无声的战斗便悄然打响。丝锥的前列如同尖锐的箭头,突破金属的阻力,逐渐深入其中。随着旋转的持续,丝锥的螺纹部分开始塑造出规整的内螺纹。在航空航天领域,丝锥的作用举足轻重。飞机的零部件往往需要极高的精度和可靠性,丝锥为这些关键部位加工出精密的螺纹连接,确保飞机在高空恶劣环境下的安全运行。每一个由丝锥加工出的螺纹,都承载着飞行的安全和使命。丝锥的制造工艺十分复杂。从原材料的选择到热处理、磨削、涂层等工序,每一个环节都需要严格的质量控制。高质量的丝锥表面光滑,刃口锋利,能够在加工过程中减少摩擦和热量的产生,从而提高加工效率和螺纹质量。而且,丝锥的保养和维护也不容忽视。使用后及时清理、涂抹防锈油,以及存放在干燥通风的环境中,都能延长丝锥的使用寿命。定期检查丝锥的磨损情况,及时更换磨损严重的丝锥,能够保证加工质量的稳定性。 精湛的工艺让这枚丝锥在攻丝过程中几乎不产生碎屑。
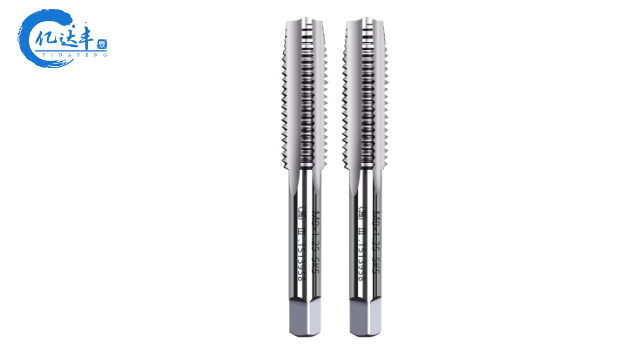
发动机部件加工:涡轮叶片螺孔加工:涡轮叶片是航空发动机的关键部件,工作环境极为苛刻,需要承受高温、高压和高速气流的冲击。钨钢丝锥可用于加工涡轮叶片上的螺孔,确保连接的可靠性。例如,在叶片与轮盘的连接部位,通过钨钢丝锥精确加工出的螺孔,能够使叶片牢固地安装在轮盘上,保证发动机在高速运转时叶片不会松动或脱落。发动机机匣螺纹孔加工:发动机机匣是发动机的外壳,起到保护内部零部件和维持发动机结构稳定性的作用。机匣通常由合金材料制成,硬度较高,普通丝锥难以满足加工要求。钨钢丝锥凭借其高硬度和耐磨性,能够在机匣上高效地加工出各种规格的螺纹孔,用于安装传感器、油管、气管等附件,为发动机的正常运行提供支持。对硬度太大的工件应该选用高规格机床丝锥。广州氮化丝锥型号
挤压丝锥与切削削不同之点为攻牙时无切削排出为其特性。浙江氮化丝锥板牙
丝锥在机械加工领域的应用广且不可或缺。在汽车制造行业中,发动机缸体、变速器壳体等零部件都需要大量的内螺纹加工。丝锥在这些部件的生产中发挥着关键作用,以确保各个连接部位的螺栓能够准确、牢固地安装。例如,发动机缸体上的油道、水道等部位的螺纹孔,需要丝锥精确加工,以保证密封性能,防止漏油、漏水等问题。在航空航天领域,对于零部件的精度和质量要求极高。
丝锥用于加工各种飞行器结构件、发动机部件中的内螺纹。由于航空航天材料往往具有强度高、高硬度等特性,如钛合金、镍基合金等,需要使用高性能的丝锥。这些丝锥不仅要保证加工精度,还要能在复杂的加工环境下保持稳定的性能,因为哪怕是微小的螺纹加工误差都可能导致严重的飞行安全隐患。 浙江氮化丝锥板牙